Laser welding machines play a crucial role in various industries due to their precision, efficiency, and versatility. However, like any other machinery, laser welding machines require regular maintenance to ensure optimal performance and longevity. Maintenance costs can add up over time, impacting the overall operating expenses of businesses. Therefore, it’s essential to implement strategies to minimize maintenance costs while maximizing machine uptime and productivity. This article discusses various strategies and best practices for reducing the maintenance costs of laser welding machines.
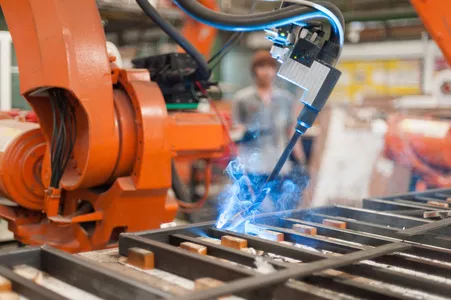
Routine Maintenance Schedule
Implement a proactive maintenance schedule for laser welding machines, including regular inspections, cleaning, and lubrication of critical components. Conduct preventive maintenance tasks such as checking optics, aligning the beam delivery system, and inspecting cooling systems to prevent potential issues before they escalate.
Operator Training and Education
Provide comprehensive training programs for operators to ensure they understand the proper operation and maintenance procedures of laser welding machines. Educate operators on identifying common maintenance issues, troubleshooting techniques, and best practices for machine care to prevent unnecessary downtime and repairs.
Optimal Machine Setup and Environment
Ensure laser welding machines are installed in a clean and well-ventilated environment to minimize the risk of contamination and overheating. Maintain stable ambient temperatures and humidity levels within the operating range specified by the manufacturer to prevent thermal stress and component degradation.
Quality Consumables and Spare Parts
Use high-quality consumables such as laser optics, nozzles, and protective lenses to maintain optimal performance and reduce the frequency of replacements. Keep an adequate inventory of critical spare parts to minimize downtime in case of unexpected failures and avoid rush orders that may incur additional costs.
Regular Performance Monitoring
Implement monitoring systems to track machine performance parameters such as power output, beam quality, and cooling system efficiency. Analyze performance data regularly to identify trends, detect early signs of potential issues, and schedule maintenance interventions proactively.
Collaboration with Suppliers and Service Providers
Establish partnerships with reputable suppliers and service providers for laser welding machine components, consumables, and maintenance services. Negotiate service contracts or maintenance agreements to access discounted rates for parts and services, reducing overall maintenance costs.
Continuous Improvement and Feedback
Encourage feedback from operators and maintenance personnel regarding machine performance, maintenance procedures, and potential improvement opportunities. Implement a continuous improvement process to address identified issues, optimize maintenance workflows, and enhance overall machine reliability and efficiency.
Lifecycle Cost Analysis
Conduct a comprehensive lifecycle cost analysis to evaluate the total cost of ownership of laser welding machines, including acquisition costs, operating expenses, and maintenance costs over the machine’s lifespan. Use the insights from the analysis to make informed decisions regarding equipment upgrades, maintenance strategies, and resource allocation to minimize long-term maintenance costs.
Conclusion
Reducing maintenance costs of laser welding machines requires a proactive approach, combining routine maintenance practices, operator training, optimal machine setup, quality consumables, performance monitoring, collaboration with suppliers, continuous improvement, and lifecycle cost analysis. By implementing these strategies and best practices, businesses can optimize the performance, reliability, and longevity of their laser welding machines while minimizing maintenance expenses and maximizing return on investment.