Laser welding machines have revolutionized manufacturing. Their precision, speed, and versatility significantly enhance production line efficiency. This article explores how laser welding machines achieve this.
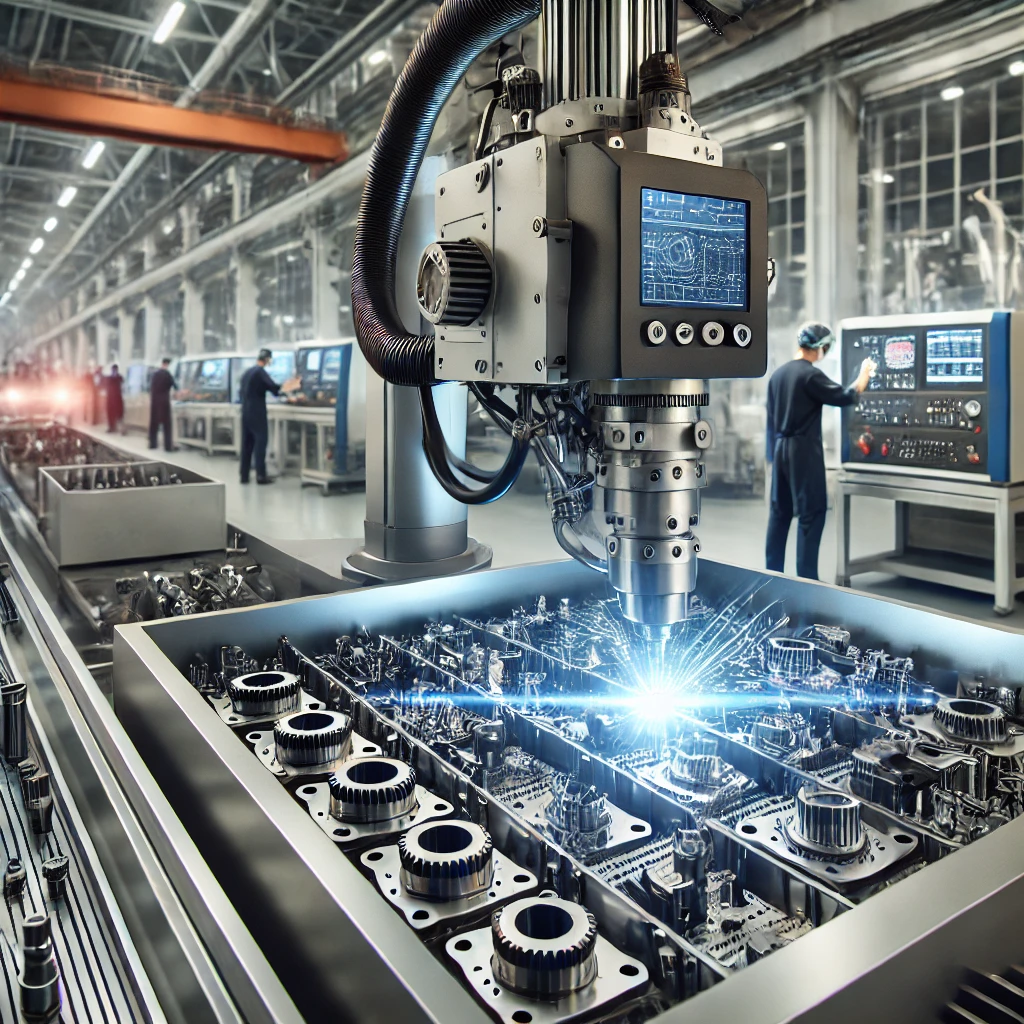
I. Precision and Accuracy
1. Unmatched Precision
Laser welding machines offer unmatched precision. They can create intricate and precise welds. This accuracy is essential for high-quality products. Traditional welding methods often lack this precision. Consequently, laser welding ensures better product consistency.
2. Consistent Quality
This precision reduces errors and waste. Consistent weld quality means fewer defects and rework. Therefore, laser welding machines contribute to a smoother production process. This improvement in quality control is vital for industries aiming to maintain high standards.
3. Application in Critical Industries
In industries like aerospace and medical device manufacturing, precision is paramount. Laser welding machines provide the exactitude needed to meet stringent standards and regulations. This reliability enhances the trust and dependability of products made with laser welding.
II. Speed and Efficiency
1. Faster Welding Times
Laser welding machines work quickly. They complete tasks in a fraction of the time required by traditional methods. Faster welding leads to faster project completion. In manufacturing, time is often critical. Delays can be costly, affecting overall production schedules and delivery timelines.
2. Enhanced Productivity
Laser welding machines boost productivity. They help companies meet tight deadlines more easily. By reducing cutting and welding time, they allow workers to handle more projects simultaneously. Consequently, they can grow their business and increase profitability. This ability to meet production demands swiftly is crucial in competitive markets.
3. Scalability
With laser welding machines, manufacturers can scale up production without significant increases in labor costs. The machines can run continuously with minimal supervision, allowing for higher output levels without compromising quality.
III. Versatility in Materials
1. Multiple Material Capability
Laser welding machines are versatile. They can weld various materials, including metals and plastics. This versatility is vital for diverse manufacturing needs. For instance, they can join different materials seamlessly. This capability allows for more complex product designs and innovative solutions.
2. Complex Product Designs
This capability allows for more complex product designs. As a result, manufacturers can expand their product range. Laser welding supports innovation in product development, enabling the creation of more advanced and diverse products.
3. Adaptability
Laser welding machines can easily adapt to different production requirements. Whether working with thin metals or thick steel plates, these machines provide consistent and reliable welds, ensuring versatility across various manufacturing sectors.
IV. Cost and Material Efficiency
1. Reduced Material Waste
Laser welding machines minimize material waste. Their precision ensures efficient material use. Less waste translates to lower material costs. Moreover, reduced waste supports environmental sustainability. Companies can achieve their green goals while saving money, which is increasingly important in today’s eco-conscious market.
2. Lower Labor Costs
Laser welding machines reduce labor costs. Faster welding means fewer hours of work. Consequently, companies spend less on wages. Additionally, one operator can manage multiple machines. This efficiency further reduces labor expenses. Over time, these savings offset the initial investment in laser welding technology.
3. Energy Efficiency
Laser welding machines are more energy-efficient than traditional welding methods. They use focused beams that require less energy to produce the same, if not better, results. This efficiency helps reduce operational costs and supports sustainable manufacturing practices.
V. Enhanced Safety
1. Improved Workplace Safety
Laser welding machines enhance workplace safety. They produce less smoke and fumes. This reduction improves air quality in the workplace. Moreover, laser welding reduces the risk of burns. Traditional welding methods involve high temperatures. Laser welding uses focused beams, minimizing heat exposure and enhancing worker safety.
2. Minimized Heat Exposure
This focus minimizes heat exposure, enhancing worker safety. Safer working conditions lead to better overall productivity. Employees can work more efficiently and comfortably in a safer environment, reducing the likelihood of accidents and improving morale.
3. Automated Safety Features
Many laser welding machines come with built-in safety features such as automatic shut-offs and sensors that detect irregularities. These features further enhance the safety of the work environment, providing an added layer of protection for operators.
VI. Automation and Innovation
1. Integration with Automation
Laser welding machines integrate well with automation. Automated systems enhance precision and efficiency. They ensure consistent, high-quality welds. Additionally, automation reduces human error. This reduction improves overall product quality. In manufacturing, automation streamlines production, making it more predictable and reliable.
2. Supporting Innovation
Laser welding machines support innovation. Their precision allows for new design possibilities. Engineers can create more efficient components. Additionally, laser welding enables advanced manufacturing techniques. These advancements drive progress in various industries. Consequently, laser welding fosters continuous improvement and innovation.
3. Advanced Manufacturing Techniques
With laser welding, manufacturers can implement advanced techniques such as additive manufacturing and hybrid welding processes. These techniques open up new possibilities for product design and functionality, pushing the boundaries of what is possible in manufacturing.
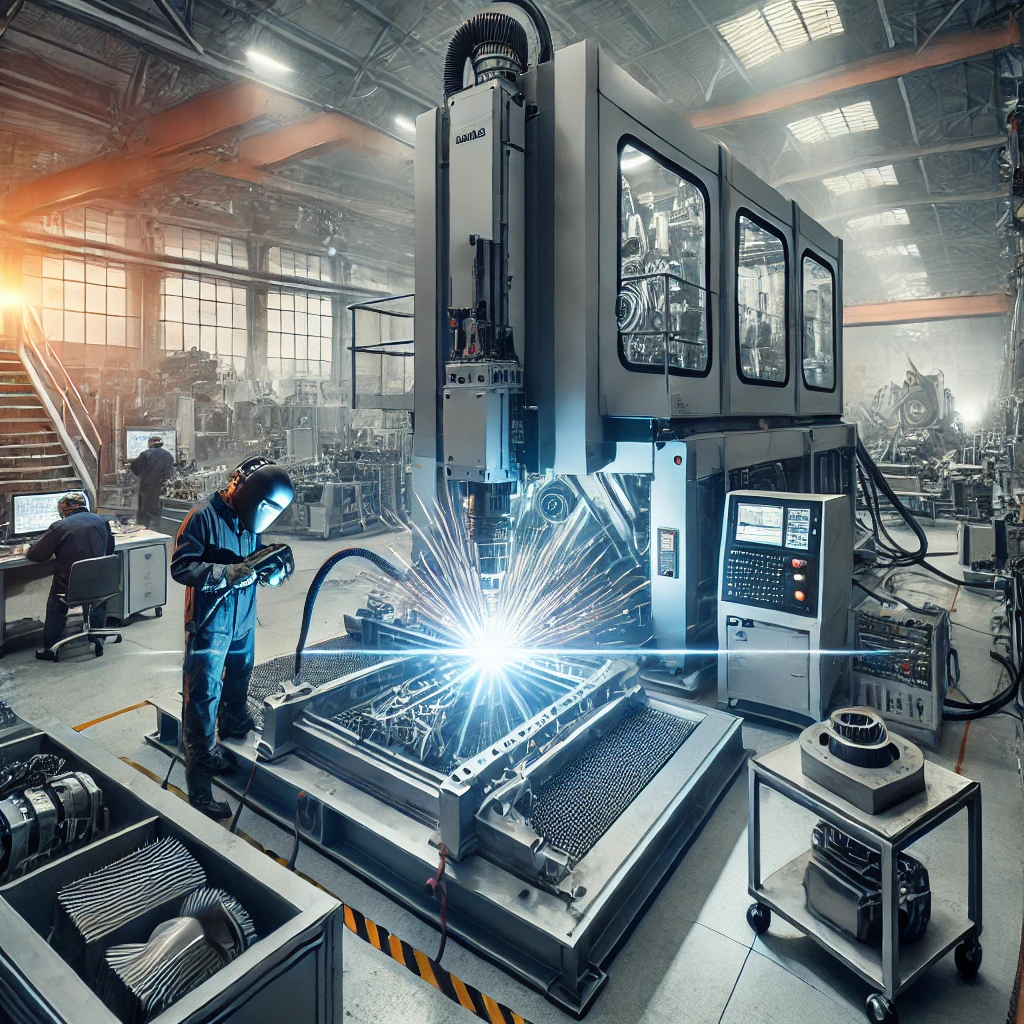
VII. Future Prospects
1. Technological Advancements
The future of laser welding in manufacturing looks promising. Technological advancements will enhance its capabilities. For instance, new laser sources will improve efficiency. Additionally, advanced control systems will enhance precision. These improvements will further support manufacturing projects.
2. Sustainable Manufacturing
These improvements will further support manufacturing projects. Consequently, laser welding will continue to play a vital role. As technology advances, their role will only grow. Therefore, laser welding machines are key drivers in modern manufacturing. Sustainable practices, supported by efficient and precise laser welding, will become increasingly critical in meeting global production demands.
3. Customization and Flexibility
Future laser welding machines will offer even greater customization options. Manufacturers will be able to tailor machines to specific production needs, increasing flexibility and efficiency. This adaptability will be crucial in a rapidly changing industrial landscape.
VIII. Conclusion
In summary, laser welding machines significantly enhance production line efficiency. Their precision, speed, and versatility make them indispensable. They ensure high-quality, durable products with minimal waste. Additionally, they reduce labor costs and improve safety. Integration with automation further boosts efficiency. As technology advances, their role will only grow. Therefore, laser welding machines are key drivers in modern manufacturing. Their continued evolution will support the advancement of industries worldwide, ensuring high standards of quality, efficiency, and sustainability.