In recent years,laser welding has revolutionized how we join materials. While traditionally used for metals, this technology has found innovative applications in plastics. The use of laser welding machines for plastic materials offers numerous advantages, including precision, speed, and strength. As industries increasingly adopt this method,laser welding devices are becoming indispensable in manufacturing.
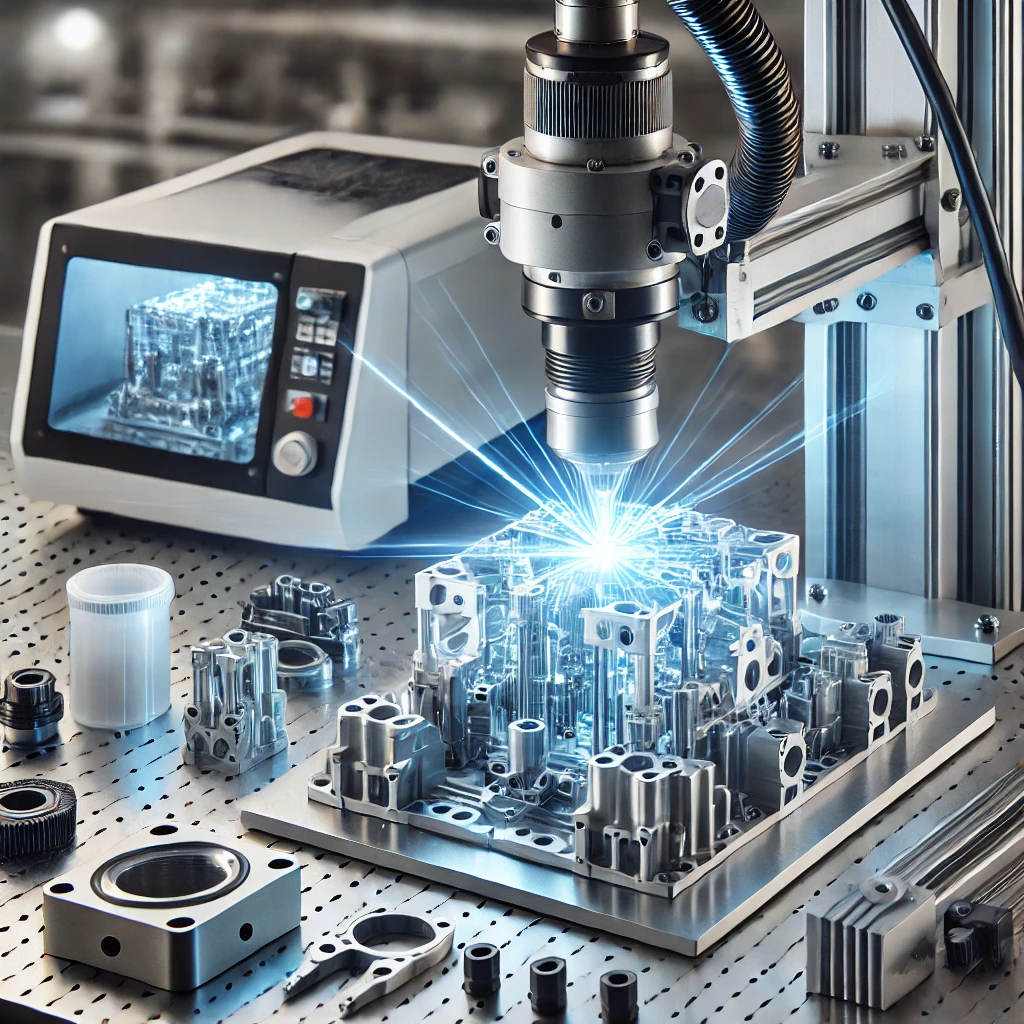
I. The Basics of Laser Welding for Plastics
Laser welding involves using a focused laser beam to join two plastic parts. This method differs significantly from traditional welding techniques. Instead of applying heat directly, the laser welding machine uses the laser’s energy to melt the plastic at the interface. The melted material then cools, forming a strong, durable bond.
Moreover,laser welding devices provide precise control over the welding process. This precision ensures that only the targeted area is affected, minimizing damage to surrounding material. Consequently,laser welding is ideal for delicate and complex plastic components.
II. Advantages Over Traditional Welding Methods
Traditional plastic welding methods, such as ultrasonic or hot plate welding, have limitations. These methods can cause significant heat distortion. In contrast,laser welding minimizes thermal damage, preserving the integrity of the plastic parts.
Additionally,laser welding machines offer higher speed and efficiency. The process can be automated, reducing labor costs and increasing production rates. This efficiency is crucial in industries like automotive, where precision and speed are paramount.
Furthermore,laser welding devices are versatile. They can join various types of plastics, including thermoplastics and composites. This versatility allows manufacturers to use laser welding across different applications, from medical devices to consumer electronics.
III. Innovations in Laser Welding Technology
Recent innovations in laser welding have expanded its capabilities in plastic manufacturing. One such innovation is the development of quasi-simultaneous welding. In this method, the laser welding machine moves the laser beam rapidly over the welding area. This movement ensures even heating and consistent weld quality.
Moreover,laser welding devices now incorporate advanced sensors and controls. These features enable real-time monitoring of the welding process. Operators can adjust parameters on the fly, ensuring optimal weld strength and quality.
Another innovation is the use of fiber lasers in laser welding. Fiber lasers offer higher power and efficiency compared to traditional CO2 lasers. They also provide better beam quality, resulting in cleaner and stronger welds. This advancement has made laser welding machines even more effective for plastics.
IV. Applications in the Automotive Industry
The automotive industry has been quick to adopt laser welding for plastic components.Laser welding machines are used to join parts like fuel tanks, air intake manifolds, and electronic housings. These components require strong, leak-proof seals, which laser welding provides.
Additionally, the precision of laser welding devices allows for the joining of complex shapes and thin-walled structures. This capability is essential as automotive designs become more intricate and lightweight materials are used. Furthermore,laser welding reduces the need for additional materials, like adhesives, lowering costs and simplifying assembly.
V. Medical Device Manufacturing
In the medical field,laser welding is used to manufacture plastic components that require strict hygiene and precision.Laser welding machines can create hermetic seals, preventing contamination in medical devices such as fluid containers, filters, and surgical instruments.
Moreover,laser welding devices ensure that the welded joints are biocompatible, which is crucial for implants and other medical devices that come into contact with the human body. The non-contact nature of laser welding minimizes the risk of introducing contaminants, making it an ideal choice for medical applications.
VI. Challenges and Solutions in Laser Welding Plastics
Despite its advantages,laser welding plastics poses challenges. One challenge is the need for compatible plastic materials. The plastics must have similar melting points for the laser welding machine to create a strong bond.
To address this, manufacturers have developed special additives that improve the absorption of laser energy. These additives allow dissimilar plastics to be welded together effectively. Additionally, new laser welding devices can adjust their settings to accommodate a wider range of materials.
Another challenge is ensuring the weld is visually appealing. In some cases, the weld line may be visible, which can be undesirable for consumer products. Innovations in laser welding now include techniques to minimize or eliminate visible weld lines. For instance, using clear or color-matched materials can make the welds nearly invisible.
VII. The Future of Laser Welding in Plastics
As laser welding technology continues to evolve, its applications in plastics will expand. Future laser welding machines will likely offer even greater precision and speed. These advancements will enable the production of more complex and high-performance plastic components.
Moreover, as environmental concerns grow,laser welding devices will play a role in sustainable manufacturing. The process is energy-efficient and produces minimal waste, aligning with the industry’s shift towards greener practices.
In addition,laser welding will likely become more accessible to smaller manufacturers. As the technology becomes more affordable, a wider range of industries will be able to adopt laser welding for their plastic components.
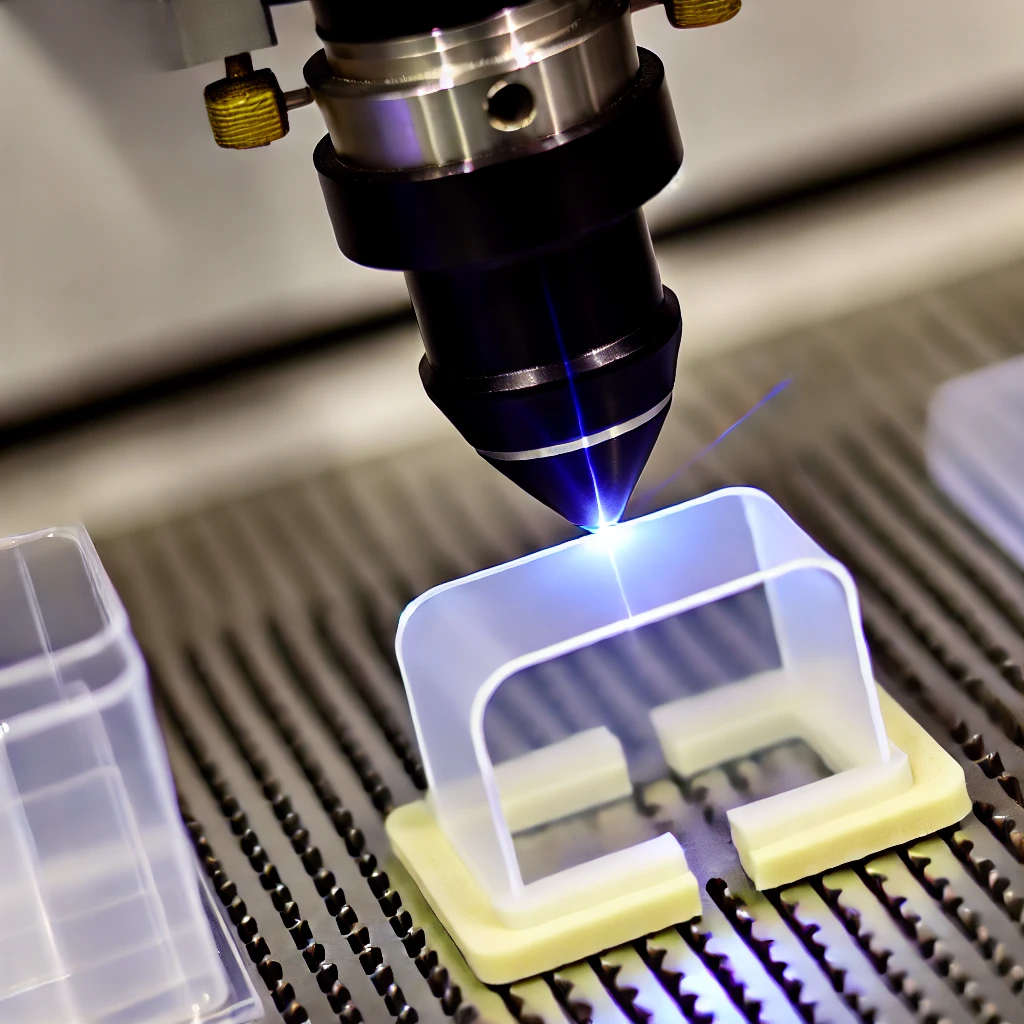
VIII. Conclusion
In conclusion,laser welding has brought significant innovations to plastic material processing. The precision, speed, and versatility of laser welding machines make them indispensable in modern manufacturing. As industries continue to innovate,laser welding devices will remain at the forefront of plastic joining technologies. The future of laser welding in plastics is bright, promising even more advancements and broader applications across various sectors.