Laser welding of plastics, due to its unique advantages, is becoming a hot topic in the field of laser welding and has attracted widespread attention in the industry. It is poised to replace traditional methods of plastic welding. This article mainly introduces the principle, application, and future prospects of plastic laser welding technology.
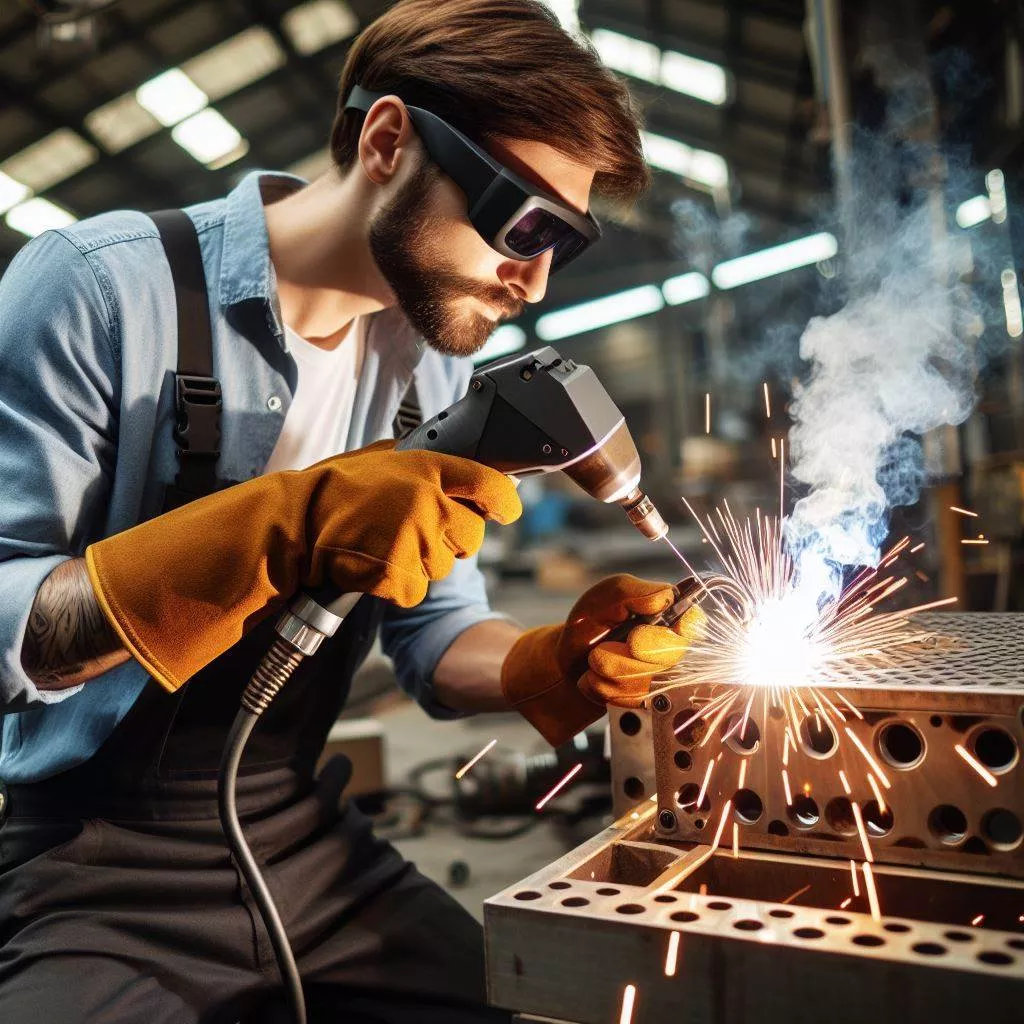
Principle of Plastic Laser Welding Technology
Main Principle
Plastic laser welding utilizes the principle of transmission welding, typically employing infrared lasers as the heat source for welding. Since lasers in the 800nm-1100nm wavelength band have a low absorption rate for the vast majority of transparent or colored thermoplastic plastics, the energy loss of the laser through the plastic is minimal. Therefore, lasers in this wavelength range are commonly chosen. Transmission welding generally uses a lap joint fixed by a clamp that can provide a certain clamping force. Additionally, the upper and lower layers of material must meet certain requirements: for the chosen laser, the upper layer of material needs to allow the laser to pass through to the maximum extent, while the lower layer needs to absorb the laser to the maximum extent. The laser passes through the upper material layer and hits the surface of the lower material layer. Due to the high absorption rate of the lower layer to the laser, a large amount of heat is generated at the joint, which is transferred from the lower to the upper material layer by heat conduction, causing the plastic at the joint to melt. Under the action of the clamping force, a secondary polymerization occurs, and a weld seam is formed at the joint after cooling, thus welding the materials together.
Various Plastic Laser Welding Methods
(a) Contour Welding
Among the welding areas of laser transmission welding, contour welding is the most “flexible,” simple, and popular technology. In this process, the laser beam is focused into a point within the welding area and moves along the contour line. The movement of the beam can be controlled by computer software, and the workpiece above it is fixed or held in place by a robotic arm. The use of robots significantly expands the range of applications for contour welding and elevates it to a position competitive with ultrasonic welding and vibration welding. The advantage of this method lies in its substantial “flexibility,” the possibility of programmable random trajectories by robots, and the control over welding diameter by changing the focal length.
(b) Simultaneous Welding
In the processing, both the welding elements and the laser beam remain stationary. First, a laser head customized for the welding area emits multiple diode laser beams simultaneously acting on the contour line, melting the welding area and thus joining the materials. The downside of simultaneous welding is the complexity of the equipment used; its lens must be specially customized according to the shape of the welding area, making it costly. It is usually used for mass welding of large parts.
(c) Quasi-Simultaneous Welding
Similar to contour welding and also to simultaneous welding, this method involves projecting the laser beam onto the welding area and scanning along the contour at high speed, several times per second, making the welding area nearly simultaneously heated and melted to form a weld seam. Therefore, the welding strength and quality depend on the laser scanning speed, the number of scanning cycles, and the laser intensity. Quasi-simultaneous welding’s advantage is its high degree of freedom and flexibility, making it particularly suitable for simple two-dimensional welding, such as mobile phone cases and electronic component casings.
(d) Mask Welding
This method uses a mask that can absorb or reflect the laser, projecting the laser beam onto the welding area and moving the laser beam or the workpiece. The target welding area melts and forms a weld seam due to the absence of a mask. Mask welding allows for the formation of weld seams wider than 10μm. In addition, mask welding is highly “flexible” because the shape of the mask determines the welding area, thus complex-shaped weld seams can also be formed using suitable masks. Mask welding precision can reach the micron level and has been applied in precision and small-size component welding, including in the medical, electronic, and electrical industries.
(e) Reflection Welding
Primarily used for circumferential line welding on cylindrical surfaces. The laser beam is projected onto the welding area after positioning by a high-speed scanning motor and is reflected a second time by a conical mirror surface, forming radial radiation on the surface of the cylindrical workpiece. The speed of the motor’s scan allows for contour welding or quasi-simultaneous welding. Reflection welding is highly productive and does not require a clamping device, making it especially suitable for cylindrical workpieces of different diameters and those that do not need to rotate.
(f) Diffraction Welding
Diffraction welding is a new type of plastic laser welding method that shapes the laser beam using diffractive optical elements and then projects the laser beam onto the welding area through a mask to heat, melt, and form a weld seam. By utilizing optical components, diffraction welding achieves spot sizes at the micron level, thus enabling micro-welding. This method can weld parts with sizes around 300μm and weld seams of 75μm, and it is also applicable to seal welding.
Advantages of Plastic Laser Welding Technology
Plastic laser welding, as a new application field in laser welding, has advantages over traditional ultrasonic welding, hot plate welding, vibration welding, and adhesive bonding in terms of cost and performance, as shown in Table 1.
Comparison with Ultrasonic Welding | Comparison with Vibration Welding | Comparison with Hot Plate Welding | Comparison with Adhesive Bonding |
No surface damage | No surface damage | No splashing, less burring | No need to add extra materials |
Low mechanical stress | Low vibration stress | Low thermal stress | Simple operation |
Low cost | Low cost | Low cost | High welding quality |
No slag | No slag | Short production cycle | Short production cycle |
The main advantages of plastic laser welding technology include:
Precise and strong weld seams, airtight and waterproof, with good sealing performance.
No residual material, allowing for close welding of parts.
As a non-contact welding method, there is no damage to the surface of the welded parts.
Flexible control through computer software to control the laser and fiber optic laser output, capable of welding small-sized or complex-shaped (even three-dimensional) products.
Significantly reduces vibration stress and thermal stress on products during the welding process, suitable for welding easily damaged products and extending product life.
Capable of welding many different types of plastic materials together, such as PC and PBT with 30% glass fiber doping.
Equipment is compact, easy to operate, low cost, and easy to maintain.
Applications and Future Prospects of Plastic Welding Technology
Application in Automotive Parts
To improve the efficiency of car engines, one method is to reduce the weight of the car body as much as possible. Materials such as plastics, resins, and special glass, due to their light weight, corrosion resistance, and stability, are increasingly used in automotive parts.
Traditionally, automotive engine intake manifolds were made of cast aluminum. Since the 1980s, due to the smooth walls, high efficiency, and light weight of plastic engine intake manifolds, they have been widely used in manifold manufacturing. Laser welding not only allows for the creation of more complex structures and shapes for intake manifolds but also ensures good welding quality, high strength, low residual stress, no welding slag, and ease of automation. Therefore, laser welding technology is gradually becoming an important welding method in the manufacturing of new plastic intake manifolds.
As society progresses, the exterior design of cars is becoming increasingly important. Tail lights, as an important functional component of cars, are showing the importance of their manufacturing process. Without changing the color of transparent materials and with good sealing, no water or air leakage, high connection strength of weld seams, and attractive appearance are achieved.
The gas-liquid separator is one of the important components of the car fuel tank system, mainly consisting of injection-molded POM upper cover and shell, which are welded together by laser welding. This method offers high process stability and high welding strength. For automotive dashboard housings, not only is an attractive appearance required, but strict demands are placed on sealability and corrosion resistance as well. Dashboards welded with plastic laser welding technology have good seam sealability and high connection strength.
Other components such as car electronic door openers, gearboxes, airbags, oil pressure sensors, and engine sensors also extensively employ plastic laser welding technology.
Application in Medical Devices
Plastic laser welding technology is primarily used in syringe systems, medical electronic devices, artificial implants, and stoma care products.
The earwax protector welded using the mask welding method is only a few millimeters in size, with the membrane and gasket tightly welded together. The non-contact nature of laser welding also ensures the sterility of the product. In high-end medical products, the Globo welding process is applied to artificial stoma care products, and for needle tip protective caps, the simultaneous welding process can be used. Welded products are environmentally friendly, and the weld seam performance is stable.
Biomedical analysis instruments require sterility and no chemical additives. Laser welding, as a non-contact welding method, has a small heat-affected zone during the welding process. Liquid analysis chips in biomedical analysis instruments, which contain micro-channel systems several centimeters long and tens to hundreds of microns wide for collecting or analyzing liquid substances, are made of plastic sheets only a few millimeters to 20 microns thick. These highly precise structures can be welded using the mask welding process.
Medical catheters require different materials and softness depending on the part of the body they come into contact with during use. Medical catheters welded using laser technology have high connection strength and good surface continuity.
Artificial hearts, some of which are made from plastic components, require welding to achieve connectivity. Laser welding, with its non-contact nature and the precision and durability of the weld seams, ensures the biocompatibility, stability, corrosion resistance, compressive strength, and sealability of the post-weld products.
Application in Electronic Device Products
For the packaging of electronic products, the welding environment and process are very important. They must meet the requirements of low dust, low heat, no strong vibrations, high packaging precision, high weld seam strength, and attractive appearance. Since a large portion of the packaging material used is plastic, plastic laser welding technology has a vast potential for development.
Sensors with fine circuits and sensing elements inside use plastic laser welding for encapsulation, resulting in excellent sealability of the casing. The casings endure well in high temperature, high humidity, dusty, and corrosive environments, and laser welding’s non-contact nature avoids vibration, significantly improving the pass rate and performance of sensor production.
Circuit boards encapsulated using laser welding technology not only have strong and sealed weld seams but also maintain high integrity and functionality.
Application in Other Areas
Laser welding of textiles, by laser stitching, provides strong and reliable seams, especially suitable for waterproof clothing and equipment requiring high air tightness.
Some industrial products’ packaging uses plastic film welding technology, achieving strong and aesthetically pleasing plastic packaging.
Future Prospects
Currently, two-dimensional plastic laser welding technology is becoming increasingly mature in terms of equipment and processes, while three-dimensional welding is still in its infancy. Therefore, the development and research of three-dimensional welding equipment and related studies on three-dimensional laser welding of plastics will become one of the future trends in plastic laser welding.
Conclusion
Due to its high welding speed, cleanliness without pollution, simplicity of equipment, absence of vibration, and no damage to the welded parts, laser welding of plastics is gradually becoming a hotspot in the field of laser welding. It has been widely used in the automotive industry, medical devices, electronic products, and other fields abroad.