Laser welding machines are sophisticated pieces of equipment used across various industries for precise metal joining applications. Proper maintenance and careful placement of these machines are essential to ensure their longevity, reliability, and optimal performance. This comprehensive article discusses the importance of maintenance and provides valuable insights into best practices for maintaining and placing laser welding machines.
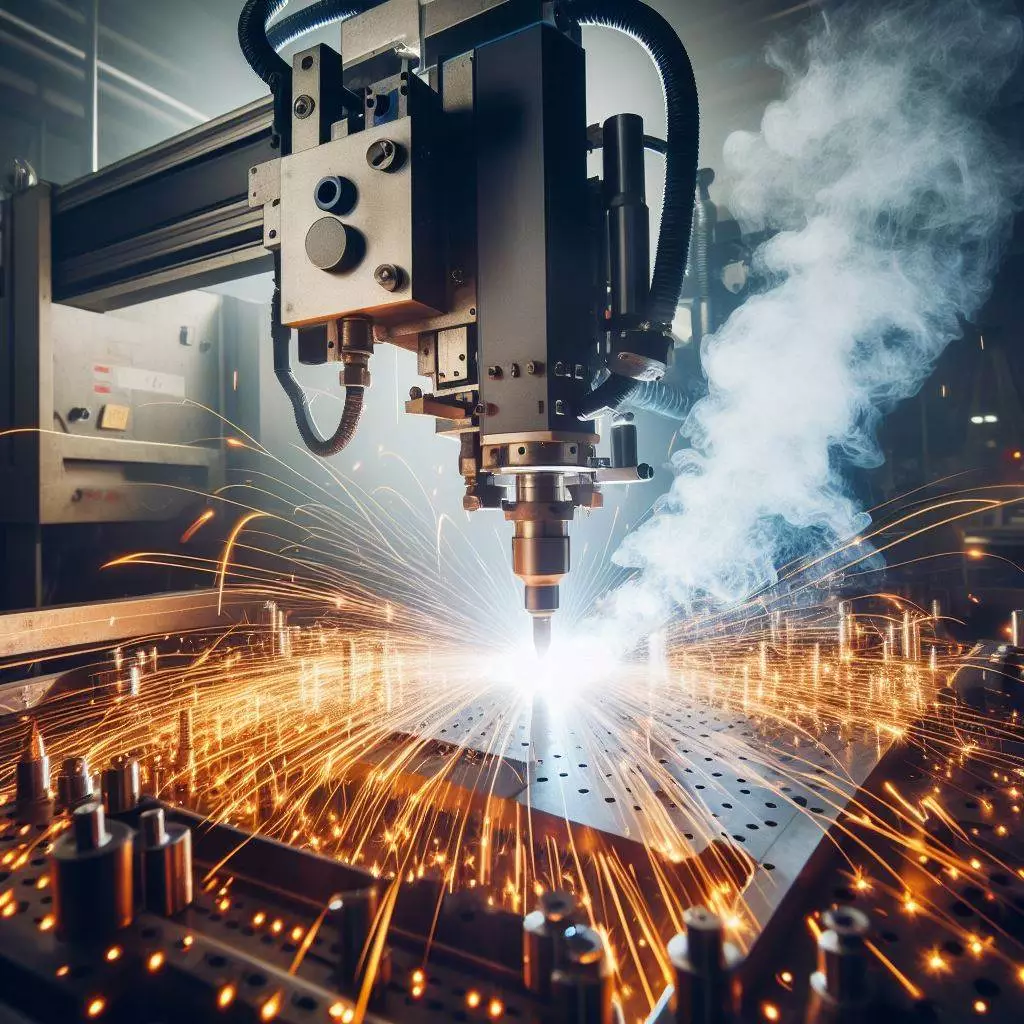
Importance of Maintenance
Laser welding machines consist of intricate components and delicate optics that require regular maintenance to ensure their functionality and performance. Regular maintenance helps prevent downtime, reduces the risk of unexpected breakdowns, and extends the lifespan of the machine. Neglecting maintenance can lead to decreased welding quality, increased repair costs, and potential safety hazards in the workplace.
Essential Maintenance Procedures
Cleaning and Inspection
Regularly clean the machine’s external surfaces, optics, and laser delivery system to remove dust, debris, and contaminants that may affect performance. Conduct routine inspections to check for signs of wear, misalignment, or damage to critical components such as optics, nozzles, and protective covers.
Lubrication
Lubricate moving parts and mechanical components according to the manufacturer’s recommendations to ensure smooth operation and minimize wear. Use recommended lubricants and follow proper lubrication procedures to avoid over-lubrication or contamination of sensitive parts.
Cooling System Maintenance
Monitor and maintain the cooling system to ensure proper temperature regulation and prevent overheating of laser components. Clean or replace filters, check coolant levels, and inspect hoses and connections regularly to prevent cooling system failures.
Scheduled Maintenance Plan
Develop a comprehensive maintenance schedule outlining specific tasks, frequencies, and responsible personnel for each maintenance activity. Incorporate preventive maintenance tasks such as optics alignment, beam quality checks, and system calibration into the schedule to maintain optimal performance.
Placement Considerations
Environmental Factors
Place the laser welding machine in a clean, well-ventilated area free from dust, smoke, and other airborne contaminants that could affect performance. Ensure adequate space around the machine for ventilation and access for maintenance activities.
Stability and Leveling
Install the machine on a stable, level surface to prevent vibrations and ensure accurate laser beam delivery during operation. Use leveling feet or adjustable mounts to achieve proper machine alignment and stability.
Electrical and Power Requirements
Ensure the machine is located near a reliable power source with sufficient voltage and current capacity to meet its electrical requirements. Use dedicated electrical circuits and surge protection devices to safeguard the machine from power fluctuations and electrical disturbances.
Safety Precautions
Implement safety measures such as interlocks, safety shields, and warning signs to protect operators and bystanders from laser hazards. Provide training to operators on safe machine operation, handling of hazardous materials, and emergency procedures in case of accidents or malfunctions.
Regular Performance Monitoring
Implement systems to monitor machine performance parameters such as power output, beam quality, and cooling system efficiency. Regularly analyze performance data to detect trends, identify potential issues, and schedule maintenance interventions proactively.
Conclusion
Proper maintenance and careful placement of laser welding machines are critical for ensuring their longevity, reliability, and optimal performance. By following best practices for maintenance procedures, developing a scheduled maintenance plan, considering placement factors, and implementing safety precautions, businesses can maximize the efficiency and lifespan of their laser welding machines while ensuring a safe working environment for operators.