Laser welding machines have become essential tools in modern manufacturing due to their high precision, efficiency, and wide range of applications. Laser welding technology, with its unique advantages, can handle a variety of welding tasks, from microelectronic components to large metal structures. This blog will explore the main application areas of laser welding machines and their distinctive characteristics in the processing field.
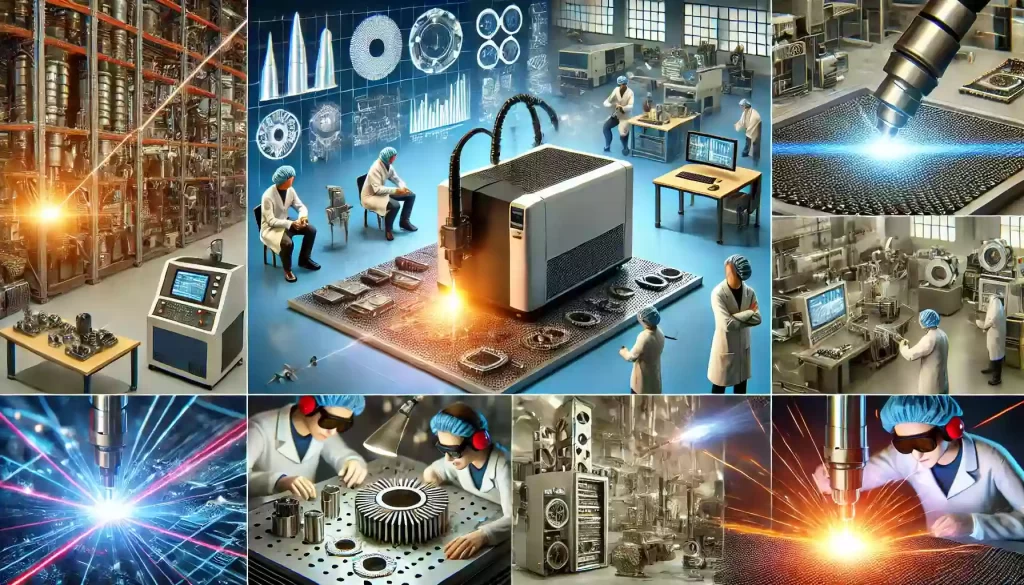
Ⅰ.Main Application Areas of Laser Welding Machines
1.Automotive manufacturing:
Laser welding technology is widely used in the automotive industry. The demand for lightweight and high-strength structures in modern automotive manufacturing has driven the adoption of laser welding technology for welding body parts and chassis structures. Laser welding machines can precisely weld different types of metals. Such as aluminum alloys and high-strength steel, enhancing the structural integrity and safety of vehicles.
Case Study: Welding of Body and Chassis
In automotive manufacturing, laser welding machines are used to weld body parts such as doors, hoods, and roofs. Their high precision and minimal heat-affected zones result in smooth surfaces, reducing the need for post-processing like grinding and finishing. Additionally, laser welding’s application in chassis welding significantly increases the strength and durability of the welded joints, improving overall vehicle safety.
2.Electronics and semiconductor industry:
In the electronics and semiconductor industry, laser welding technology is used to weld precise electronic components and microconnections. Laser welding machines can operate with micron-level accuracy, making them suitable for welding integrated circuits, sensors, and microelectronic devices. Their non-contact processing method effectively avoids mechanical damage to sensitive components.
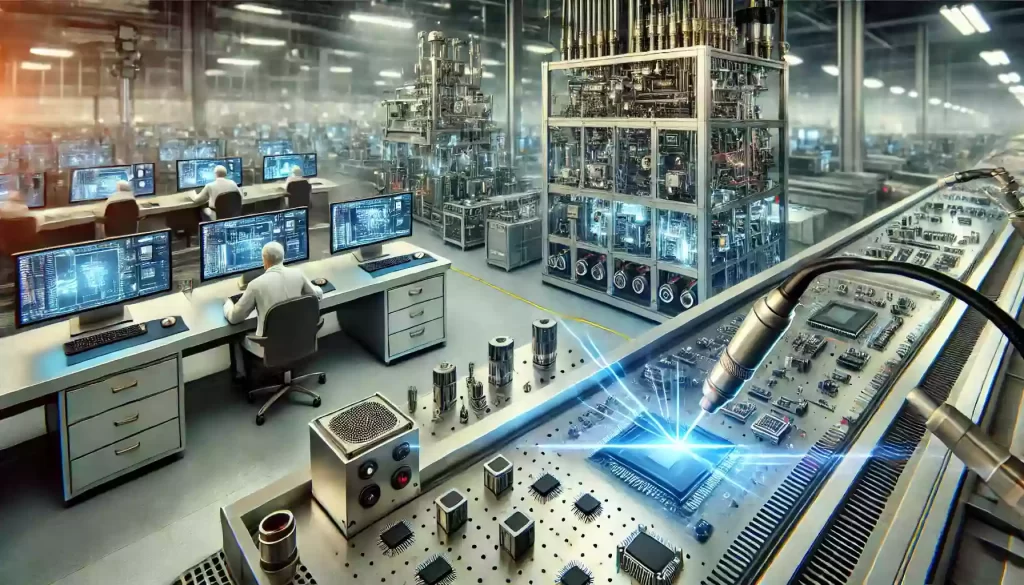
Case Study: Welding of Microelectronic Components
Laser welding machines can precisely weld tiny leads and connections in microelectronic components. Their high energy density and controlled heat input ensure the accuracy and stability of the welding area, resulting in good conductivity and durability of the welded electronic components.
3.Medical device manufacturing:
Laser welding technology also plays a vital role in medical device manufacturing. Given the high cleanliness and precision requirements of medical devices, laser welding machines are the ideal choice. They can weld materials such as stainless steel and titanium alloys to produce complex medical instruments and implants.
Case Study: Manufacturing of Surgical Instruments and Implants
In the production of surgical instruments and implants, laser welding machines provide seamless welding, avoiding contamination and defects common with traditional welding methods. For example, laser welding in the manufacture of titanium orthopedic implants ensures a smooth, defect-free surface, ensuring the safety and reliability of implants within the human body.
4.Aerospace industry:
Laser welding technology is used in the aerospace industry to manufacture high-precision and high-strength aerospace components. Due to the high efficiency and low distortion characteristics of laser welding, it can meet the stringent requirements of aerospace materials, welding complex shapes, and difficult-to-process high-temperature alloys.
Case Study: Welding of Aerospace Engine Components
Laser welding plays a crucial role in the production of aerospace engine components. It can weld thin-walled structures and complex alloy materials, ensuring the strength and reliability of the welded joints. Laser welding enables lightweight design of engine components, enhancing overall engine performance and efficiency.
5.Precision instruments and watchmaking industry
Laser welding technology is applied in the precision instruments and watchmaking industry to weld small and precise metal parts. Its high precision and non-contact welding characteristics allow laser welding to accurately join complex mechanical structures and decorative details without damaging the parts.
Case Study: Welding of Watch Movements and Cases
In watch manufacturing, laser welding is used to join intricate movement components and case structures. Its high precision and controllability result in welded cases and movements with excellent decorative effects and mechanical performance, enhancing the overall quality and aesthetics of watches.
Ⅱ.Processing Characteristics of Laser Welding Machines
1.High precision and low heat-affected zone:
Laser welding machines achieve extremely high welding precision, crucial for high-precision parts requiring strict dimensional control. Due to the concentrated heat input of laser welding, the heat-affected zone is minimal, effectively reducing welding distortion and thermal stress.
2.Non-contact processing:
Laser welding is a non-contact processing method, meaning there is no mechanical contact during welding, which prevents physical damage to the workpiece surface. This characteristic is particularly suitable for processing fragile, precise, and complex parts, ensuring the quality and integrity of the welded joints.
3.High efficiency and controllability:
Laser welding machines can complete welding tasks in a very short time, providing high processing efficiency. Their welding parameters (such as laser power, welding speed, and focal position) can be precisely controlled, ensuring a stable and reliable welding process suitable for various complex welding requirements.
4.Multi-material compatibility:
Laser welding technology can process a variety of different materials, including metals, alloys, and some non-metallic materials. It can automatically adjust parameters during welding to accommodate different material properties, providing consistent welding quality across various materials.
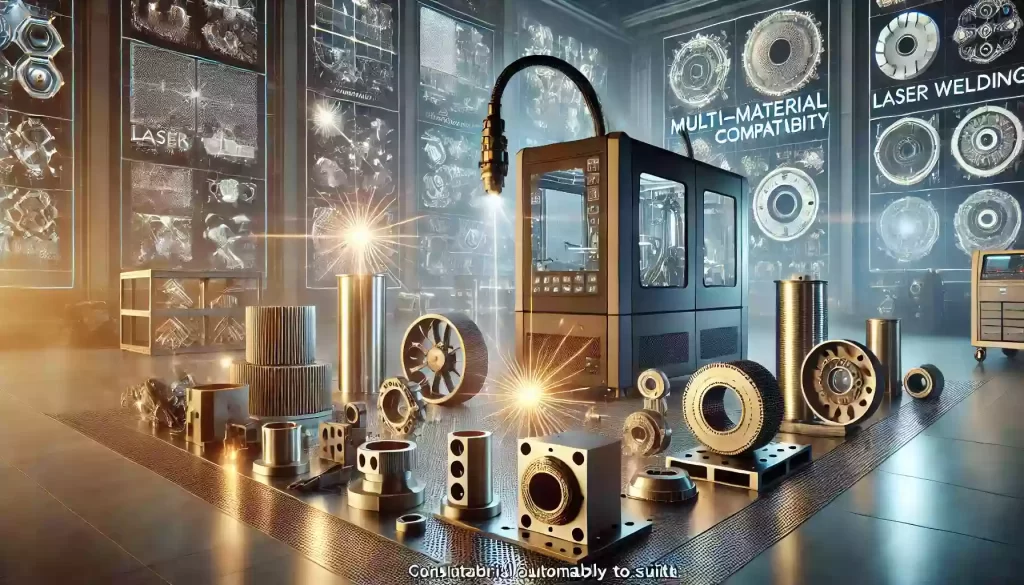
Final Thoughts
Laser welding machines, with their high precision, efficiency, and wide material compatibility, have become indispensable tools in modern manufacturing. Whether in automotive manufacturing, electronic components, medical devices, aerospace, or precision instruments, laser welding machines demonstrate their unique advantages and application potential. As technology continues to evolve and innovate, laser welding machines will play an even greater role in more fields and applications, driving the manufacturing industry towards greater efficiency and precision.