With the rapid development of manufacturing and continuous technological advancements, handheld welding technology is becoming increasingly favored by manufacturers. Particularly, handheld laser welding machines offer significant competitive advantages by enhancing welding quality and production efficiency. This article will delve into how handheld welders, especially handheld laser welding machines, have become an ideal choice for manufacturers, and analyze their unique advantages and broad application prospects in detail.
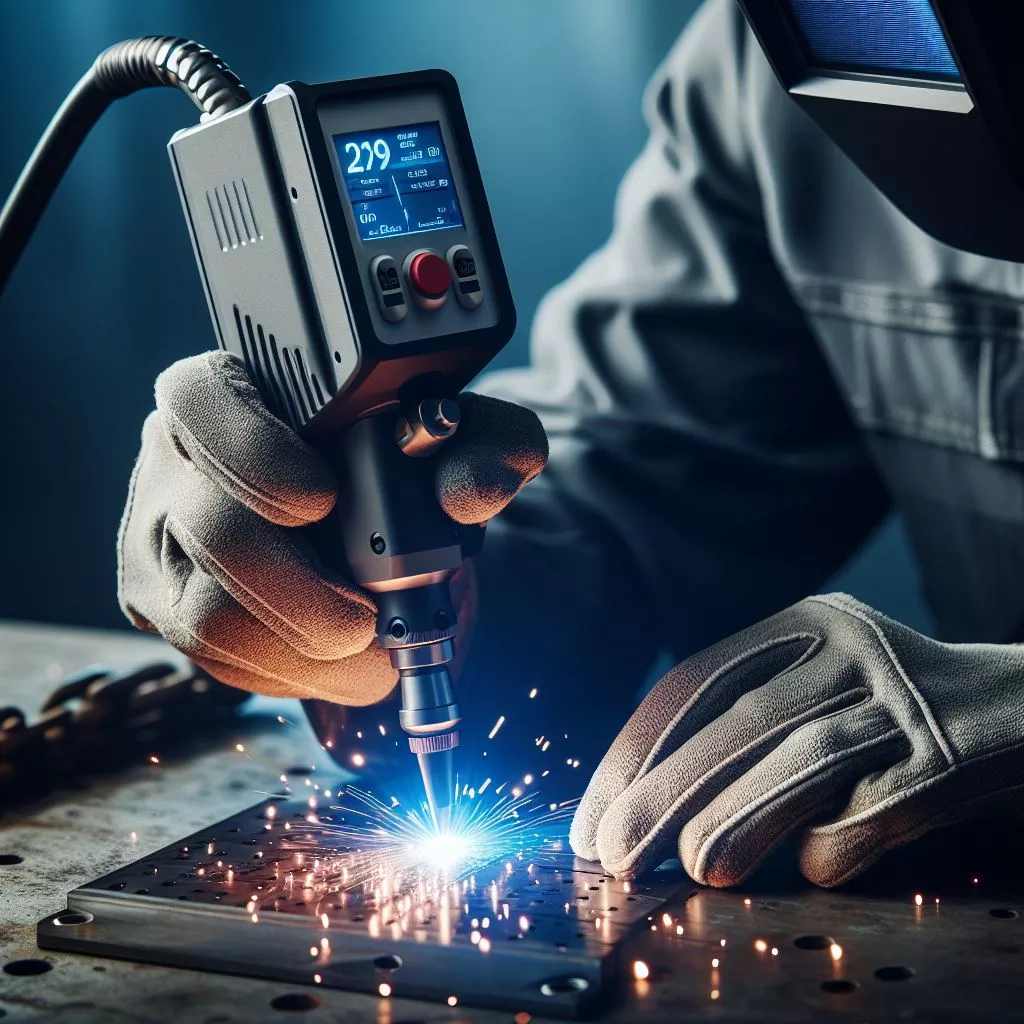
Limitations of Traditional Welding Technologies
In the past, manufacturers mainly relied on traditional welding technologies such as MIG (Metal Inert Gas) welding and TIG (Tungsten Inert Gas) welding. However, these traditional methods have evident limitations. For example, TIG welding requires experienced operators and tends to deform thin materials due to high heat input. MIG welding, although faster, requires the use of consumable wire, and has strict requirements for material pre-treatment and joint design, limiting its application range. Additionally, traditional welding methods are challenging to operate in vertical positions and perform poorly when welding metals of different thicknesses.
As market demands change, manufacturers urgently need to find more efficient and flexible welding solutions to address rising production costs and the shortage of skilled workers. According to the American Welding Society, the United States will face a shortage of 375,000 skilled welders by 2023, further highlighting the urgency of improving welding efficiency and reducing operational complexity.
Advantages of Handheld Laser Welding
The advent of handheld laser welding machines provides manufacturers with an excellent solution. Compared to traditional welding methods, laser welding has numerous unique advantages:
Efficient Production
Handheld laser welding machines weld at four times the speed of traditional MIG and TIG welding. This high efficiency not only increases productivity but also significantly reduces production cycles, helping manufacturers fulfill orders faster and meet market demands.
Precise Control
Laser welding technology utilizes high-energy-density laser beams to achieve precise control over the welding process. This results in more stable welding quality and more aesthetically pleasing welds. Additionally, the ability to control heat input effectively reduces thermal deformation, making it feasible to weld thin materials.
Multi-Material Compatibility
Laser welding is not limited to steel; it can also weld aluminum, copper, and other metals. Even dissimilar metal welding (bimetal welding) can be easily achieved. This greatly expands its application range, making it suitable for more manufacturing scenarios.
Automation and Collaborative Robot Applications
Handheld laser welding technology can be combined with collaborative robots (cobots) to further enhance production automation. Cobots can perform repetitive welding tasks in factories, reducing the burden on workers and improving production consistency and quality. The flexibility of handheld laser welding combined with the multifunctionality of cobots makes it especially suitable for small-batch, high-mix production environments.
Ease of Operation with Handheld Laser Welding
Many manufacturers may worry about the complexity and learning curve of laser welding technology. However, modern handheld laser welding systems typically come with preset parameters and are very user-friendly. For common material types and thicknesses, simply select the corresponding preset parameters to begin welding. This simplicity not only reduces the skill requirements for operators but also enables novices to quickly get started, enhancing production efficiency.
Additionally, handheld laser welding systems usually feature user-friendly interfaces and safety measures to ensure safe operation. Operators only need to follow the guidelines in the equipment manual to safely and efficiently complete welding tasks.
Welding Quality and Reliability
Handheld laser welding not only delivers aesthetically superior welds but also ensures welding strength and reliability, as validated by authoritative institutions. Third-party tests have shown that handheld laser welding on various thicknesses of stainless steel plates revealed no cracks, incomplete fusion, porosity, or other defects, and all weld profiles passed tests, meeting AWS D17.1:2017 Class A standards. This demonstrates that handheld laser welding can provide both aesthetically pleasing welds and strong, reliable joints.
Additional Functions and Applications
Handheld laser welding machines are not limited to welding but can also be used for part cleaning and passivation. The laser cleaning function can remove oil and debris from workpiece surfaces, improving welding quality. The laser passivation function can prevent post-weld corrosion, enhancing the durability of welded parts. These additional functions further enhance the practicality and value of handheld laser welding machines, providing manufacturers with more application possibilities.
Safety and Usage Guidelines
Although handheld laser welding machines have many built-in safety features, they remain high-energy industrial equipment requiring strict adherence to safety protocols during operation. For example, operators should wear protective clothing, use safety goggles suitable for the laser type, and perform welding tasks within a designated laser-controlled area. Additionally, operators must be familiar with the safety requirements and operational outlined in the equipment manual to ensure the safety of the welding process.
Economic Viability of Handheld Laser Welding
While early laser welding systems were expensive, advancements in technology and increased production scale have significantly reduced the cost of handheld laser welding machines. This makes advanced technology affordable for more small and medium-sized manufacturers, enhancing their production capabilities and competitiveness.
Moreover, the high efficiency and low maintenance cost of handheld laser welding machines also save manufacturers a substantial amount of production and operational expenses. For example, modern fiber lasers have a wall-plug efficiency of up to 50%, significantly reducing energy consumption and cooling requirements, thereby lowering operational costs. Additionally, the high speed and quality of laser welding increase output and reduce scrap rates, thus improving profit margins.
Future Prospects of Handheld Laser Welding in Manufacturing
Handheld laser welding technology not only offers significant competitive advantages to manufacturers today but also holds promising future prospects. As technology continues to advance, the efficiency and quality of laser welding will further improve, and its application range will expand. For example, with the development of 3D printing technology, handheld laser welding can be used for post-processing 3D printed metal parts, improving their surface quality and structural strength.
Additionally, as smart manufacturing and Industry 4.0 progress, handheld laser welding will integrate with Internet of Things (IoT) and Artificial Intelligence (AI) technologies, achieving more intelligent and automated production processes. This will further enhance the production efficiency and quality control levels in manufacturing, providing manufacturers with greater competitive advantages.
Conclusion
Handheld laser welding technology offers manufacturers a welding solution that combines high efficiency, high quality, and multifunctionality. Compared to traditional welding methods, handheld laser welding significantly improves production efficiency and welding quality while simplifying operation and reducing the skill requirements for operators. Its multi-material compatibility and automation potential make it widely applicable in modern manufacturing.
By adopting handheld laser welding technology, manufacturers can address the challenges of skilled labor shortages, enhance production efficiency and product quality, and stand out in a competitive market. Therefore, handheld laser welding is undoubtedly an important choice for manufacturers to achieve sustainable development in the future.