In the modern fabrication landscape, laser welding technology has emerged as a revolutionary method, offering substantial advantages over traditional welding techniques. This article explores the comparative benefits of using laser welding machines for steel materials, highlighting efficiency, precision, and quality enhancements.
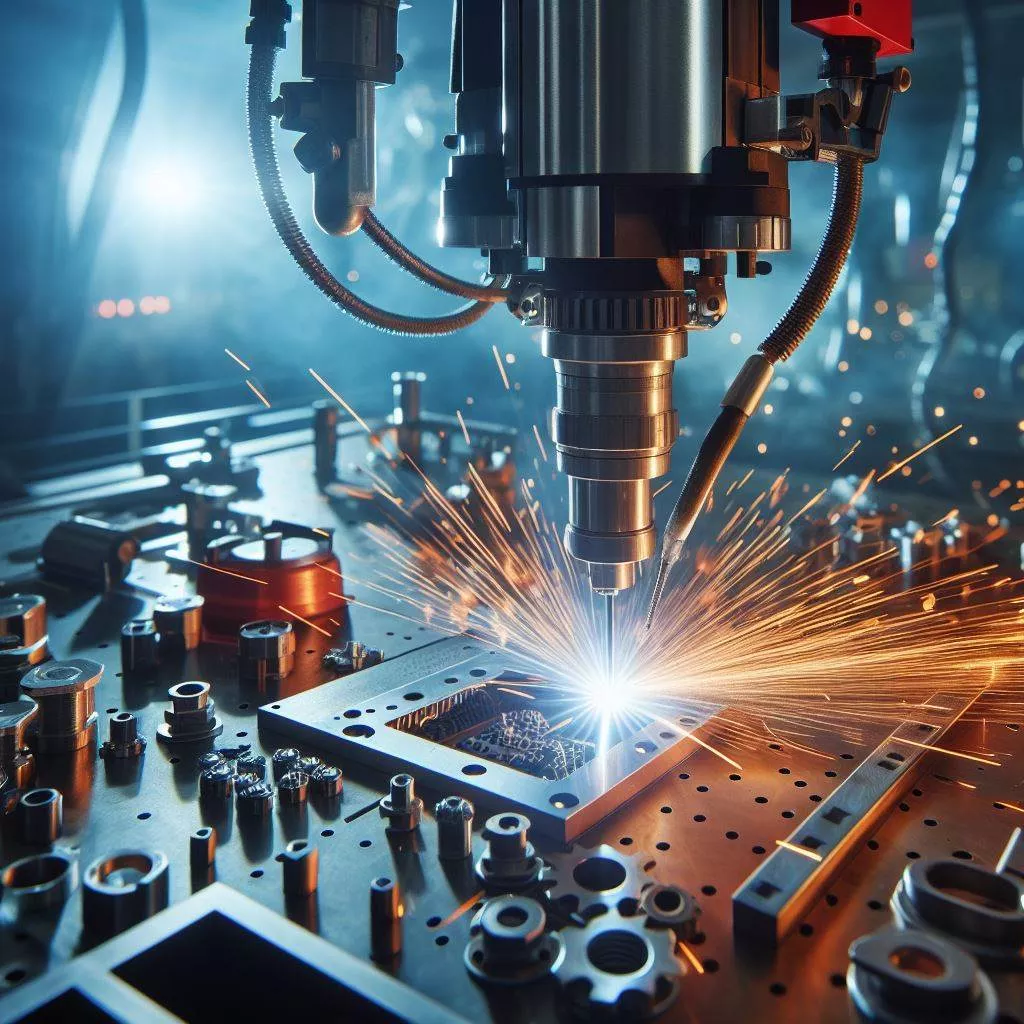
Precision and Quality
Laser welding stands out for its incredible precision. Utilizing a highly focused laser beam, this method allows for pinpoint accuracy, which is especially beneficial in applications requiring intricate work on small or detailed components. Unlike traditional welding, which can lead to warping and other distortions due to higher heat input, laser welding minimizes thermal distortion, ensuring higher part accuracy and integrity.
Efficiency and Speed
Laser welding machines significantly enhance operational efficiency. They can operate at speeds up to ten times faster than conventional welding techniques such as TIG (Tungsten Inert Gas) or MIG (Metal Inert Gas) welding. This speed does not compromise the weld’s quality, making it ideal for mass production environments where time and throughput are critical factors.
Versatility
Another notable advantage of laser welding is its versatility. Lasers can effectively weld a variety of steel types and thicknesses, often without the need to change tooling. Furthermore, laser welding can be easily automated and integrated into digital manufacturing systems, allowing for more consistent and repeatable results across production batches.
Reduced Heat Affected Zone (HAZ)
The Heat Affected Zone (HAZ) in laser welding is significantly smaller compared to traditional methods. This results in less alteration of the material properties adjacent to the weld, which is crucial for maintaining the strength and durability of the steel. The reduced HAZ also decreases the likelihood of material fatigue and failure under stress.
Environmental Impact
Laser welding is a cleaner process. It generates less waste and emissions than traditional welding, due to the absence of filler materials and shielding gases in many of its applications. This not only makes it an environmentally friendlier option but also reduces the overall cost associated with waste management and environmental compliance.
Economic Considerations
Initially, the investment in laser welding technology can be higher than traditional welding setups. However, the long-term benefits due to increased productivity, reduced rework, and lower operating costs provide a substantial return on investment. Additionally, the decrease in consumable use, such as filler materials and gases, contributes to ongoing savings.
Conclusion
Laser welding machines offer significant advantages over traditional welding techniques when working with steel materials. Their precision, efficiency, versatility, and reduced environmental impact make them a superior choice in many industrial applications. As industries continue to advance towards more sustainable and efficient manufacturing processes, laser welding is set to become increasingly prevalent in steel fabrication.