Laser welding machines are sophisticated tools used in various industries for joining metal components with precision and efficiency. Understanding the intricate working principles of these machines is crucial for optimizing their performance and applications. This article provides a comprehensive analysis of the working principles of laser welding machines, delving into the underlying physics, components, and processes involved
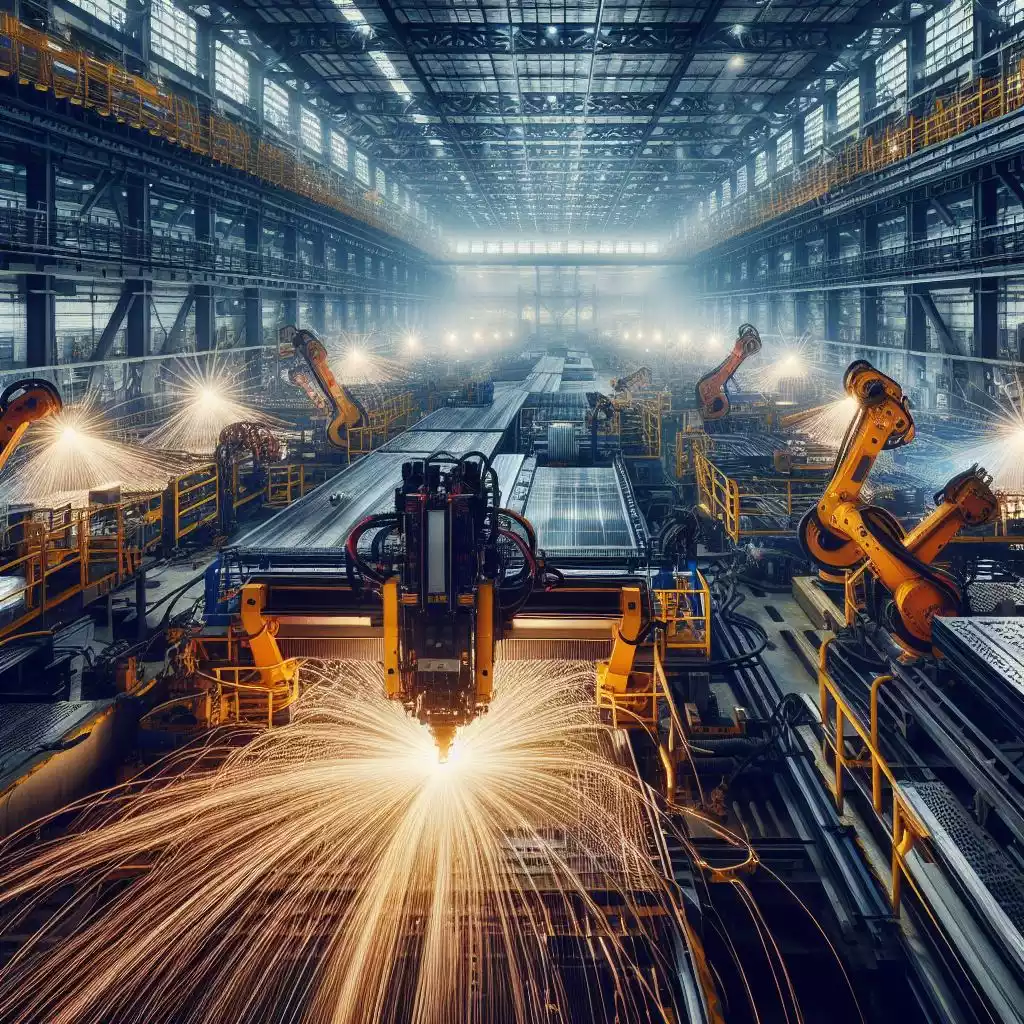
Fundamentals of Laser Welding
Laser welding is a process that utilizes the energy of a focused laser beam to melt and fuse metal components together. The fundamental principle behind laser welding lies in the conversion of electrical or optical energy into a highly concentrated beam of coherent light. This beam is then directed onto the workpiece, where it generates intense heat at the weld point, leading to localized melting and bonding of the metal.
Laser Generation and Amplification
The heart of a laser welding machine is the laser source, which generates and amplifies the laser beam. Different types of lasers are used in laser welding, including solid-state lasers (such as Nd:YAG and fiber lasers) and gas lasers (such as CO2 lasers). These lasers operate based on various mechanisms of energy conversion and amplification, such as stimulated emission and optical resonators.
Beam Delivery System
Once generated and amplified, the laser beam is delivered to the work piece through a beam delivery system. This system typically consists of mirrors and lenses that focus and direct the laser beam with precision onto the desired welding area. The quality and stability of the beam delivery system play a critical role in achieving consistent and high-quality welds.`
Interaction with the Work piece
Upon reaching the work piece, the focused laser beam interacts with the material, initiating a series of physical and thermal processes. The laser beam’s energy is absorbed by the material’s surface, leading to rapid heating and localized melting. The material undergoes phase changes from solid to liquid state, forming a molten pool at the weld point.
Weld Pool Dynamics
The dynamics of the weld pool, including its size, shape, and behavior, are influenced by various factors such as laser power, welding speed, material properties, and beam parameters. Proper control of these parameters is essential for achieving desired weld characteristics, including penetration depth, bead shape, and fusion zone morphology.
Solidification and Bond Formation
As the laser beam moves along the weld joint, the molten metal solidifies behind it, forming a metallurgical bond between the joined components. The rapid cooling rate associated with laser welding results in fine microstructures and narrow heat-affected zones, contributing to the mechanical strength and integrity of the weld.
Process Monitoring and Control
Real-time monitoring and control of the laser welding process are essential for ensuring weld quality and consistency. Various monitoring techniques, such as infrared thermography, spectroscopy, and vision-based systems, are employed to assess key parameters such as temperature distribution, weld bead geometry, and defect detection. Feedback from these monitoring systems enables adjustments to welding parameters in real time, optimizing the welding process.
Advancements and Future Directions
Ongoing research and development in laser welding technology continue to push the boundaries of what is achievable in terms of speed, precision, and versatility. Advancements in laser sources, beam delivery systems, process monitoring techniques, and automation are driving improvements in productivity, quality, and cost-effectiveness. Additionally, the integration of artificial intelligence and machine learning algorithms holds promise for further enhancing process control and optimization in laser welding.
Conclusion
In conclusion, laser welding machines operate based on sophisticated principles of laser generation, beam delivery, material interaction, and process control. Understanding the intricacies of these principles is essential for optimizing the performance and capabilities of laser welding machines across various applications. With ongoing advancements and research in laser welding technology, the future holds exciting prospects for further improving the efficiency, precision, and versatility of laser welding processes.