In the realm of modern manufacturing, laser welding stands out for its precision, efficiency, and versatility. However, the high initial cost of laser welding machines poses a significant barrier for many businesses, particularly small and medium-sized enterprises. This article explores actionable strategies to reduce the financial burden of acquiring this transformative technology, enabling more companies to leverage the benefits of laser welding.
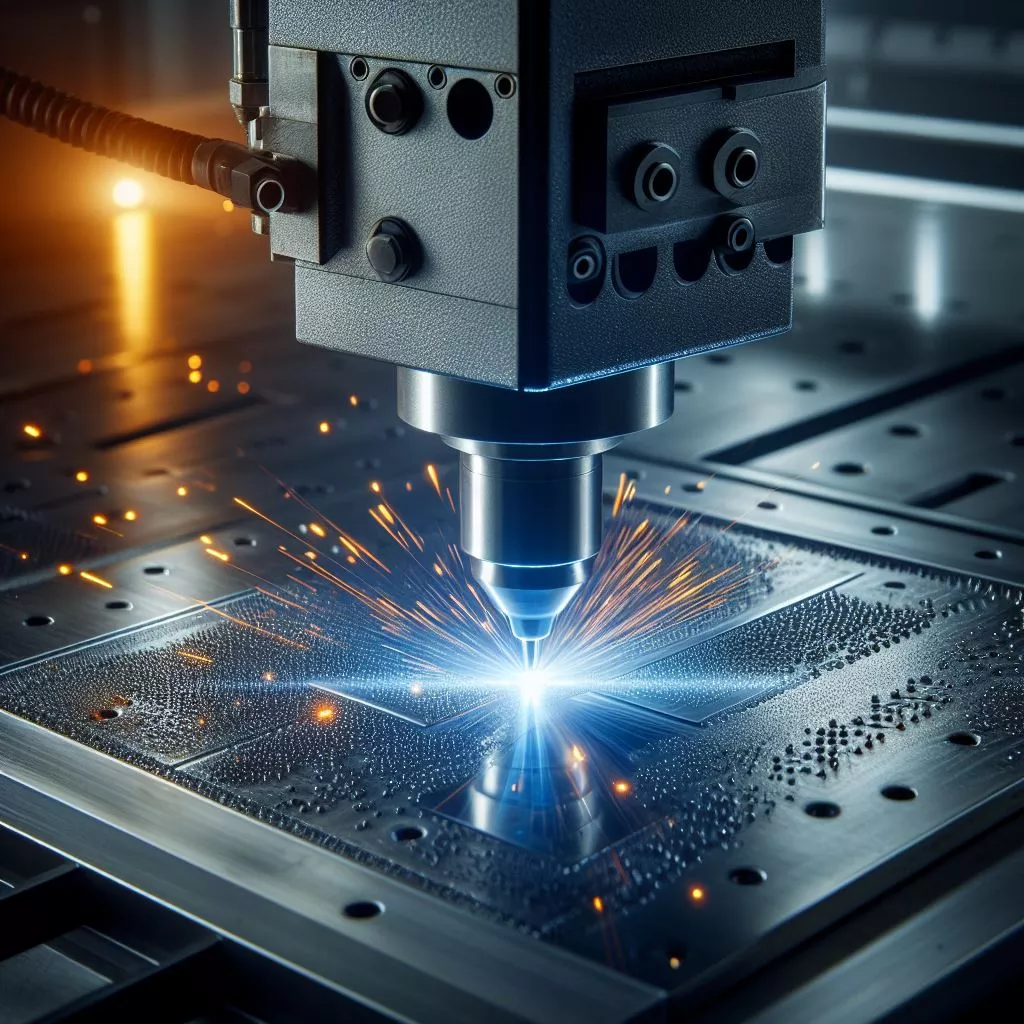
Understanding Laser Welding Technology
Laser welding uses a concentrated beam of light to melt and fuse materials together, offering unmatched accuracy and speed. Compared to traditional welding techniques, it minimizes heat damage, allows for the welding of dissimilar materials, and enhances productivity. The main types of laser welding machines include fiber lasers, CO2 lasers, and crystal lasers, each suited to different materials and applications.
Strategies for Reducing Initial Purchase Costs
Buying Used or Refurbished Machines
One effective way to lower initial expenses is by purchasing used or refurbished laser welding machines. Many suppliers offer certified pre-owned equipment that has been thoroughly inspected and serviced, providing a cost-effective alternative to new models.
Choosing Machines with Only Necessary Features
While advanced features can enhance capabilities, they also increase the price. Carefully assess your specific needs and opt for a machine that includes only those features essential to your operations, avoiding the premium for unnecessary technology.
Negotiating with Suppliers
Don’t hesitate to negotiate with suppliers. Asking for discounts, package deals, or favorable financing terms can lead to significant savings. Building a good relationship with suppliers may also unlock additional perks such as free training or extended warranties.
Optimizing Operational Efficiency
Training Staff for Optimal Operation
Investing in comprehensive training for your team ensures that the machine is used efficiently, reducing waste and maximizing output. Well-trained operators can also identify and troubleshoot minor issues before they escalate into costly repairs.
Regular Maintenance to Prevent Costly Repairs
Adhering to a strict maintenance schedule prolongs the life of the machine and prevents expensive downtime. Regular check-ups can identify wear and tear early, allowing for timely repairs that circumvent major malfunctions.
Choosing Energy-Efficient Models
Energy-efficient laser welding machines may have a higher upfront cost but can lead to substantial savings on electricity bills in the long run. Look for models with energy-saving features and consider the long-term financial benefits.
Leveraging Financing and Tax Incentives
Exploring Financing Options
Financing options, such as loans or leasing, can spread the cost of the machine over time, making it more manageable. This approach also preserves capital for other business needs.
Taking Advantage of Government Tax Incentives
Many governments offer tax incentives, rebates, or grants for companies investing in technology upgrades. Research available programs in your region, as they can significantly offset the purchase cost.
Considerations for Long-Term Savings
Investing in Quality for Durability
Choosing a high-quality laser welding machine may cost more initially but results in lower lifetime costs due to its durability and reduced need for repairs. Prioritize reliability and build quality in your selection process.
Evaluating Total Cost of Ownership
Beyond the purchase price, consider the total cost of ownership, including maintenance, repair, and operational costs. A cheaper machine that requires frequent repairs and consumes more energy may be more expensive in the long run.
Future-Proofing with Scalable Machines
Investing in scalable laser welding machines that can adapt to future needs is a wise strategy. Look for models that allow for upgrades or expansions, such as increased power, larger working areas, or additional features. This adaptability can save costs over time by avoiding the need to purchase new machines as your business grows or as technology advances.
Case Studies and Success Stories
Examples of Businesses that Successfully Reduced Their Costs
Many businesses have navigated the challenge of high initial costs for laser welding machines and found innovative ways to minimize their expenses. For instance, a small automotive parts manufacturer opted for a refurbished fiber laser welding machine, saving 40% off the price of a new model without compromising on performance. Another example is a metal fabrication startup that took advantage of government grants for small businesses investing in green technologies, significantly reducing their upfront costs.
Lessons Learned and Best Practices
These success stories highlight several best practices:
Thorough research and due diligence before making a purchase can uncover opportunities for savings.
Investing in training and maintenance extends the life of the machine and enhances its resale value.
Exploring financial assistance and tax incentives can provide unexpected relief to budget constraints.
Conclusion
Reducing the costs of purchasing a laser welding machine is achievable through a combination of strategic planning, informed decision-making, and taking advantage of available resources. By considering the total cost of ownership, opting for machines with only necessary features, and leveraging financing and tax incentives, businesses can make laser welding technology accessible and affordable. It is crucial to stay informed about the latest advancements and market opportunities, ensuring that you invest wisely and reap the maximum benefits from your laser welding equipment. As the manufacturing landscape evolves, the ability to adapt and innovate will be key to success. Therefore, carefully evaluate your options, seek advice from industry experts, and make informed decisions that will drive your business forward in the competitive world of modern manufacturing.