Laser welding machine is an advanced equipment. It uses a high-energy laser beam to weld metals or other thermoplastic materials together. Compared with traditional welding methods, laser welding has many unique advantages. Such as high precision, high speed and low heat-affected zone. However, it also has some limitations. This article will introduce the working principle of laser welding machine in detail and explore its advantages and disadvantages.
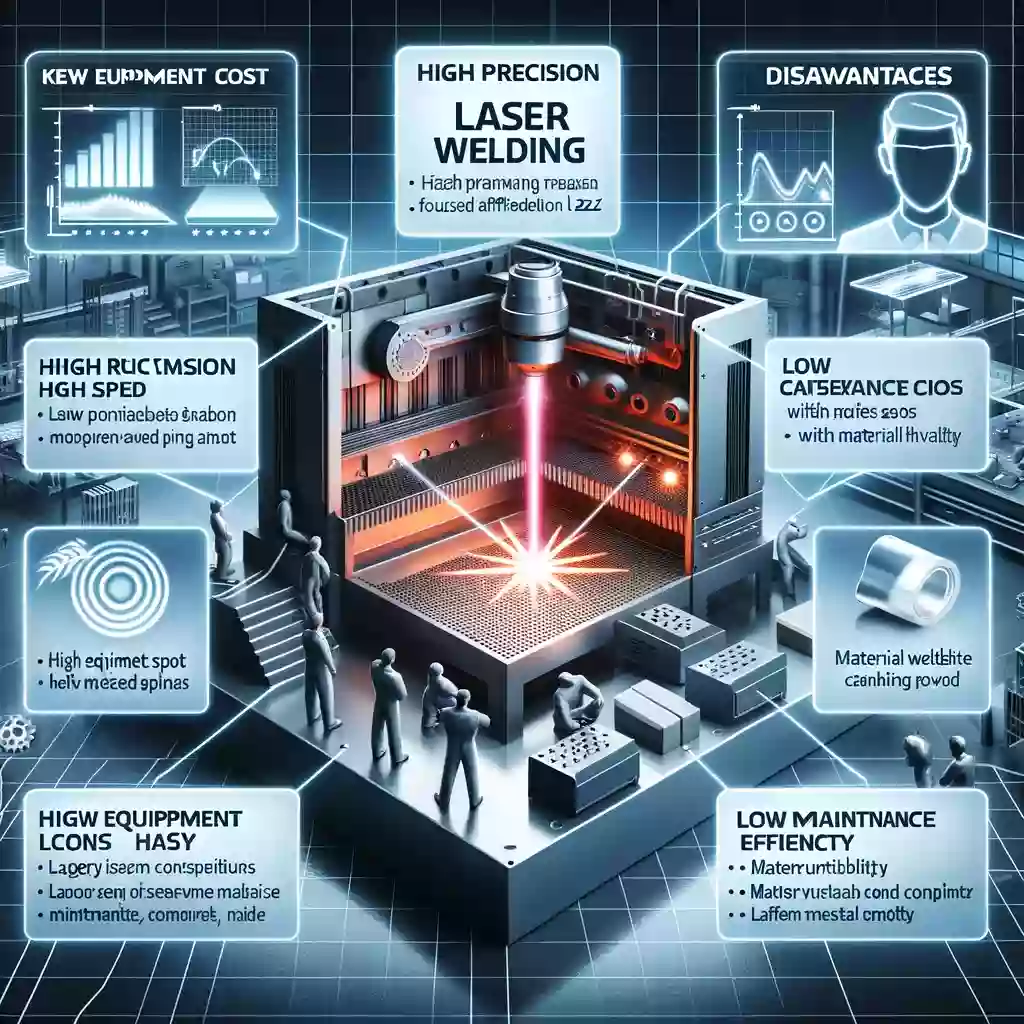
Ⅰ.Working Principle of Laser Welding Machine
The core principle of laser welding machine is to use the high energy density of the laser beam to locally heat and melt the material to achieve welding. The laser beam is generated by a laser generator and forms a high-energy spot after being focused by an optical system. When the laser beam is irradiated to the surface of the workpiece, the material absorbs the laser energy and quickly heats to the melting point to form a molten pool. As the laser beam moves, the molten pool moves and solidifies in the welding area to form a weld.
Ⅱ.Types of Laser Welding Machine
1.Conduction welding:
The energy density of the laser beam is low. And the heat is mainly transferred to the inside of the workpiece through heat conduction to form a weld. This method is suitable for welding thin plate materials, with a large weld width but a shallow depth.
2.Deep-melting welding:
The energy density of the laser beam is high. And it can form a deep-melting hole on the surface of the workpiece. The laser beam is transmitted through the hole to the deeper inside of the workpiece to form a deep and narrow weld. Deep-melting welding is suitable for welding thick plate materials, and the welding depth can reach several millimeters or even deeper.
Ⅲ.Advantages of Laser Welding Machine
1.High precision:
The spot size of laser welding is small, the energy density is high, and it can achieve precise control at the micron level. It is particularly suitable for welding precision parts, such as electronic components, medical devices, etc.
2.High speed:
The welding speed of laser welding is fast, which can usually reach several to dozens of times that of traditional welding methods, significantly improving production efficiency.
3.Low heat-affected zone:
Due to the concentrated energy of laser welding, the heat-affected zone (HAZ) is small, which reduces the thermal deformation and thermal stress of the material, and is particularly suitable for welding heat-sensitive materials and thin plates.
4.High degree of automation:
The laser welding machine is easy to combine with the CNC system to realize automated production. Through programming, the welding path and parameters can be precisely controlled, which is suitable for mass production and welding of complex shapes.
5.Non-contact processing:
Laser welding does not require contact with the workpiece, avoiding the wear and contamination of electrodes or welding wires in traditional welding, and the welding quality is stable.
6.Material diversity:
Laser welding is suitable for a variety of materials, including carbon steel, stainless steel, aluminum alloy, titanium alloy, etc., and can also achieve welding of dissimilar materials.
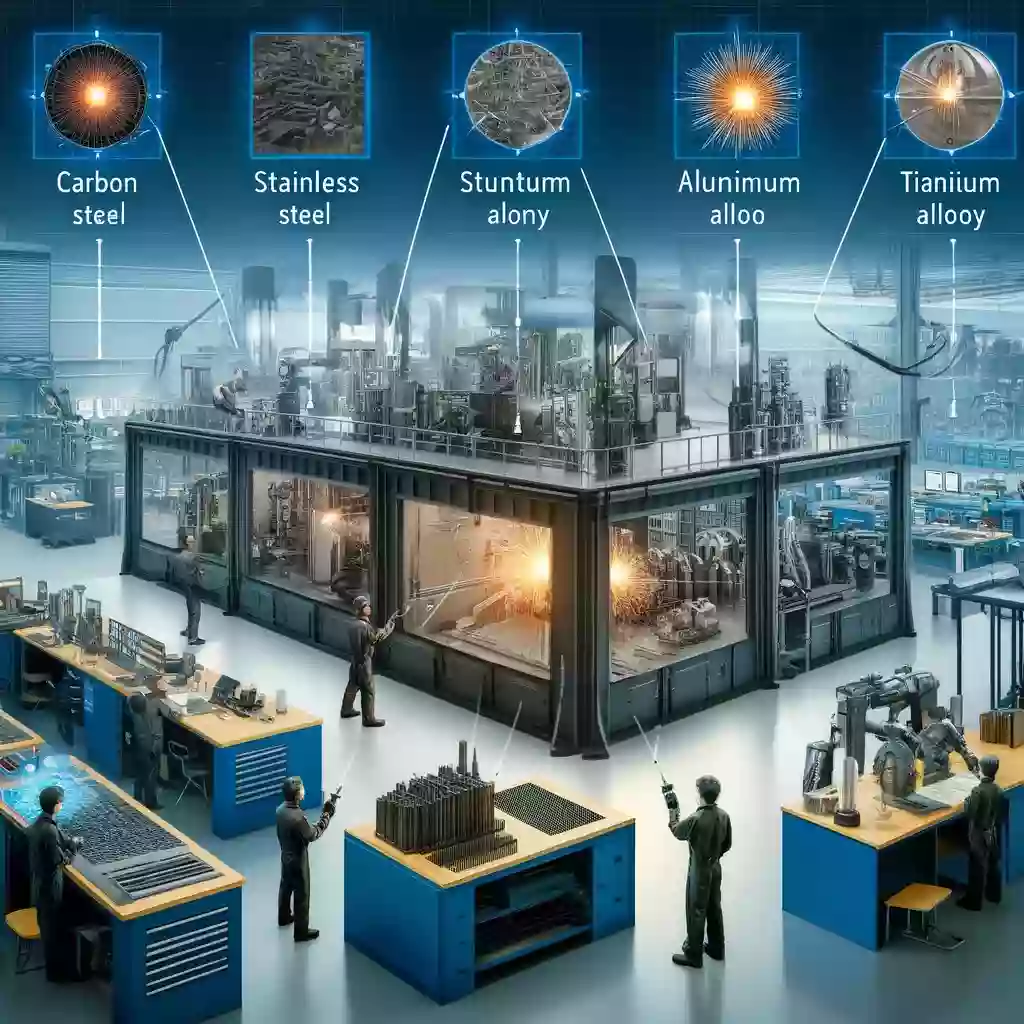
Ⅳ.Disadvantages of Laser Welding Machine
1.High equipment cost:
The equipment cost of laser welding machine is relatively high, especially high-power laser and precision control system, which makes the initial investment larger. This may be an obstacle for small enterprises or projects with limited funds.
2.Low energy conversion efficiency:
The energy conversion efficiency of laser welding is relatively low. Usually only 10% to 30% of the laser energy can be converted into effective welding heat, and the rest is lost as heat energy and light energy, affecting the overall energy efficiency.
3.High requirements for the operating environment:
Laser welding needs to be carried out in a clean and dust-free environment to avoid contaminating the laser light path and welding area, which increases the requirements for the production environment.
4.Complex maintenance:
The maintenance of laser welding machine is relatively complicated, and professional technicians are required to perform regular maintenance and calibration, which increases the maintenance cost.
5.Not suitable for some materials:
Although laser welding is suitable for a variety of materials, for some high reflectivity and high thermal conductivity materials (such as copper, silver, etc.), the welding effect is not good, and special process measures are required.
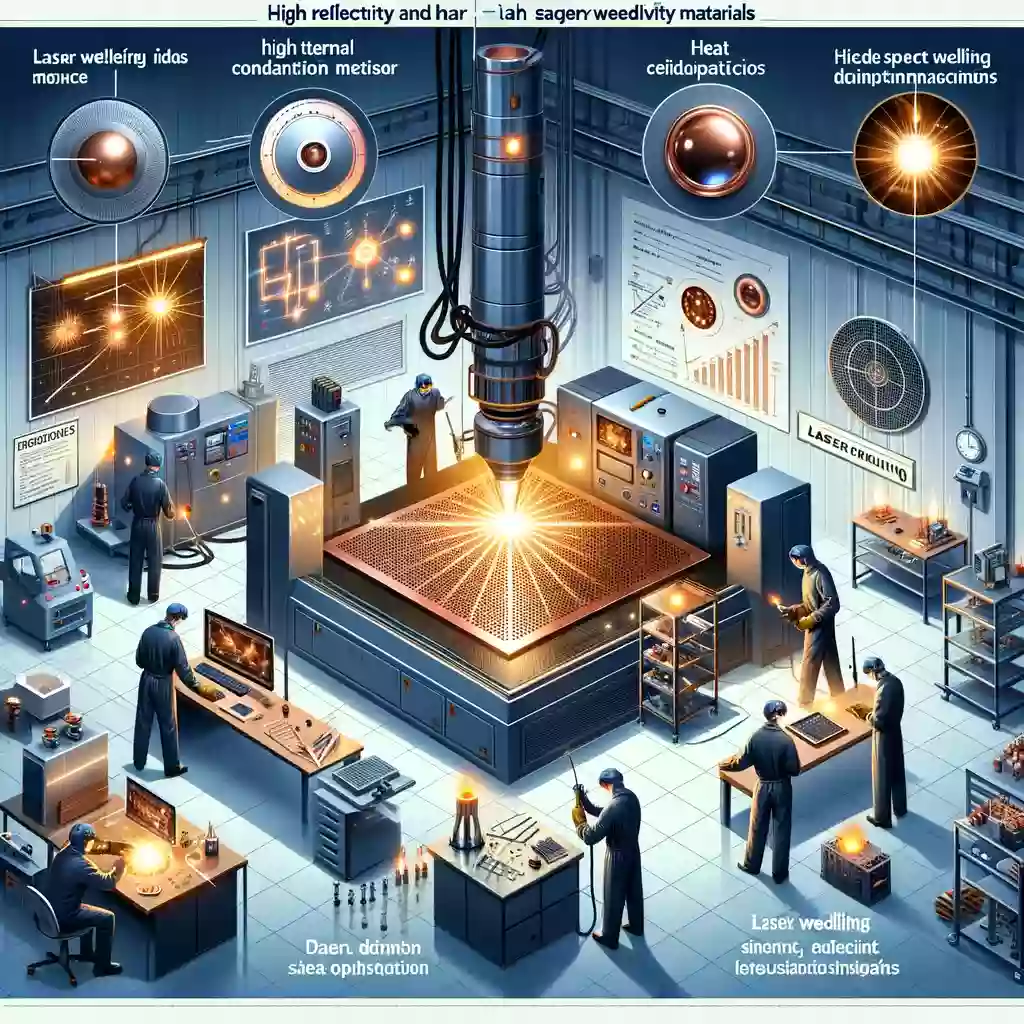
Final Thoughts
As an advanced welding technology, laser welding machine has been widely used in many industrial fields due to its advantages such as high precision, high speed and low heat affected zone. However, its disadvantages such as high equipment cost and low energy conversion efficiency also limit its application in some occasions. Therefore, when choosing laser welding technology, it is necessary to comprehensively consider its advantages and disadvantages, and make reasonable decisions based on specific application requirements. Through continuous technological innovation and cost optimization, laser welding technology will play a greater role in more fields.