In modern manufacturing, welding technology is an indispensable part. With the advancement of science and technology, welding technology is also developing continuously. As a new type of welding tool, laser welding machine has gradually entered people’s field of vision and has shown its unique advantages in many fields. So, what are the differences between laser welding machine and traditional welding machine? This article will make a detailed comparison from multiple aspects.
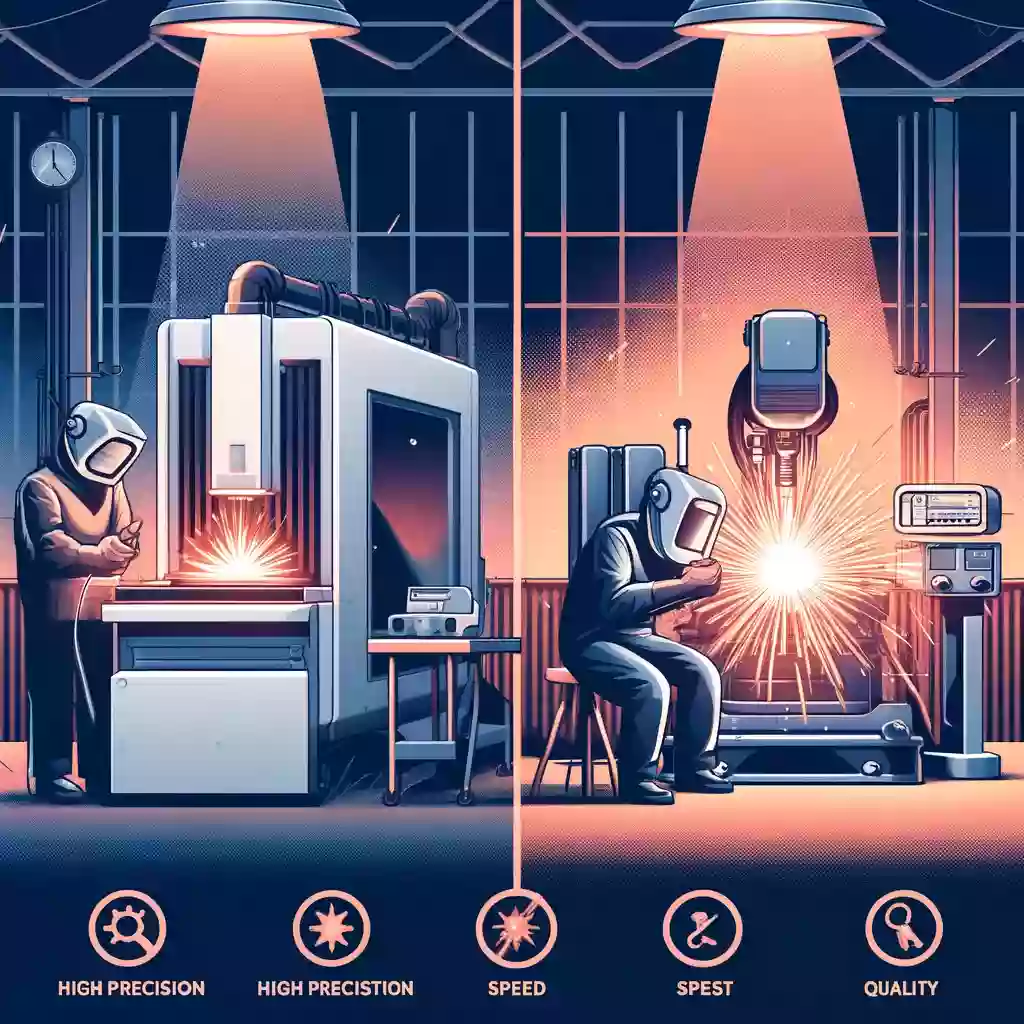
Ⅰ. Working Principle
1. Laser welding machine uses high energy density laser beam
Laser welding machine uses high energy density laser beam to irradiate the surface of the workpiece, so that the material melts and solidifies quickly to form a firm welding point. Laser welding has the characteristics of high efficiency, precision and non-contact, and is suitable for welding materials of various complex shapes.
2. Traditional welding machine uses arc, flame or resistance
Traditional welding machines mainly rely on arc, flame or resistance heating to melt and connect welding materials. Common traditional welding methods include arc welding, gas welding and resistance welding. These methods generally have problems such as large heat-affected zone and uneven heat input, which can easily lead to material deformation and increased internal stress.
Ⅱ. Welding Accuracy
1. The welding accuracy of laser welding machine is extremely high
Laser welding machine has extremely small laser beam diameter, concentrated energy and extremely high welding accuracy. Laser welding can achieve micron-level welding, which is particularly suitable for welding precision parts, such as electronic components, micro sensors, etc. The heat-affected zone of laser welding is small and the material deformation is extremely small, so it has obvious advantages in high-precision manufacturing.
2. The welding accuracy of traditional welding machine is relatively low
In contrast, the welding accuracy of traditional welding machine is relatively low. Traditional welding usually produces a large heat-affected zone, which is easy to cause workpiece deformation, especially when welding thin plate materials or precision parts. This problem is particularly prominent. Therefore, in occasions where high-precision welding is required, laser welding machine is obviously more advantageous.
Ⅲ. Welding Speed
1. Laser welding machine can complete the welding of a welding spot in just a few seconds
The welding speed of laser welding machine is fast and efficient. Due to the high energy density of laser welding and the rapid welding process, it usually takes only a few seconds or even less to complete the welding of a welding spot. This makes laser welding have great advantages in mass production and can significantly improve production efficiency.
2. The welding speed of traditional welding machines is slow
The welding speed of traditional welding machines is relatively slow, especially for welding of large areas or thick materials, which takes a long time to complete. This not only affects production efficiency, but may also increase production costs. Therefore, for manufacturing industries that require fast and efficient welding, the advantages of laser welding machines are more obvious.
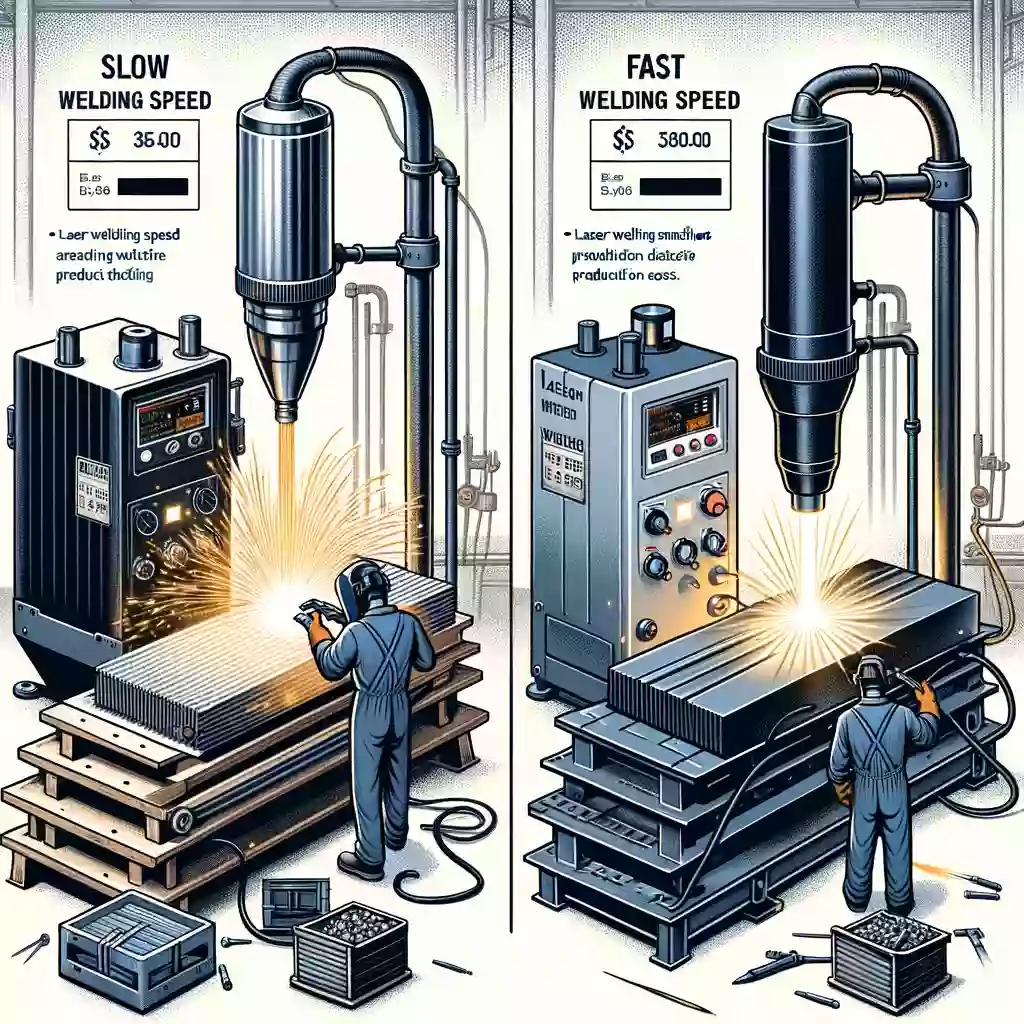
IV. Applicable Materials
1. Laser welding machines can process most metal materials
Laser welding machines can weld almost all metal materials, including some materials with high melting points and high hardness, such as titanium alloys, stainless steel, etc. In addition, laser welding can also weld some dissimilar metals that are difficult to process by traditional methods, making material selection more flexible.
2. Traditional welding machines can only process some materials
Traditional welding machines are limited in the selection of welding materials. Some materials with high melting points or easy oxidation are difficult to achieve high-quality welding effects through traditional welding methods. In addition, the welding of dissimilar metals is also more difficult in traditional welding, and it is easy to produce welding defects and quality problems.
V. Welding Quality
1. High welding quality of laser welding machines
The laser welding machine has high welding quality, beautiful and smooth welds, and no subsequent processing is required. Laser welding has low heat input, small changes in physical and chemical properties of the welding area, high weld strength and good corrosion resistance. Therefore, laser welding is widely used in aerospace, automobile manufacturing, medical equipment and other fields with extremely high welding quality requirements.
2. The welding quality of traditional welding machines is rough
The welding quality of traditional welding machines is relatively low, and the welds are rough, which may require subsequent treatment such as grinding and polishing. In addition, traditional welding is prone to welding defects such as pores and cracks, which affect the welding quality and service life.
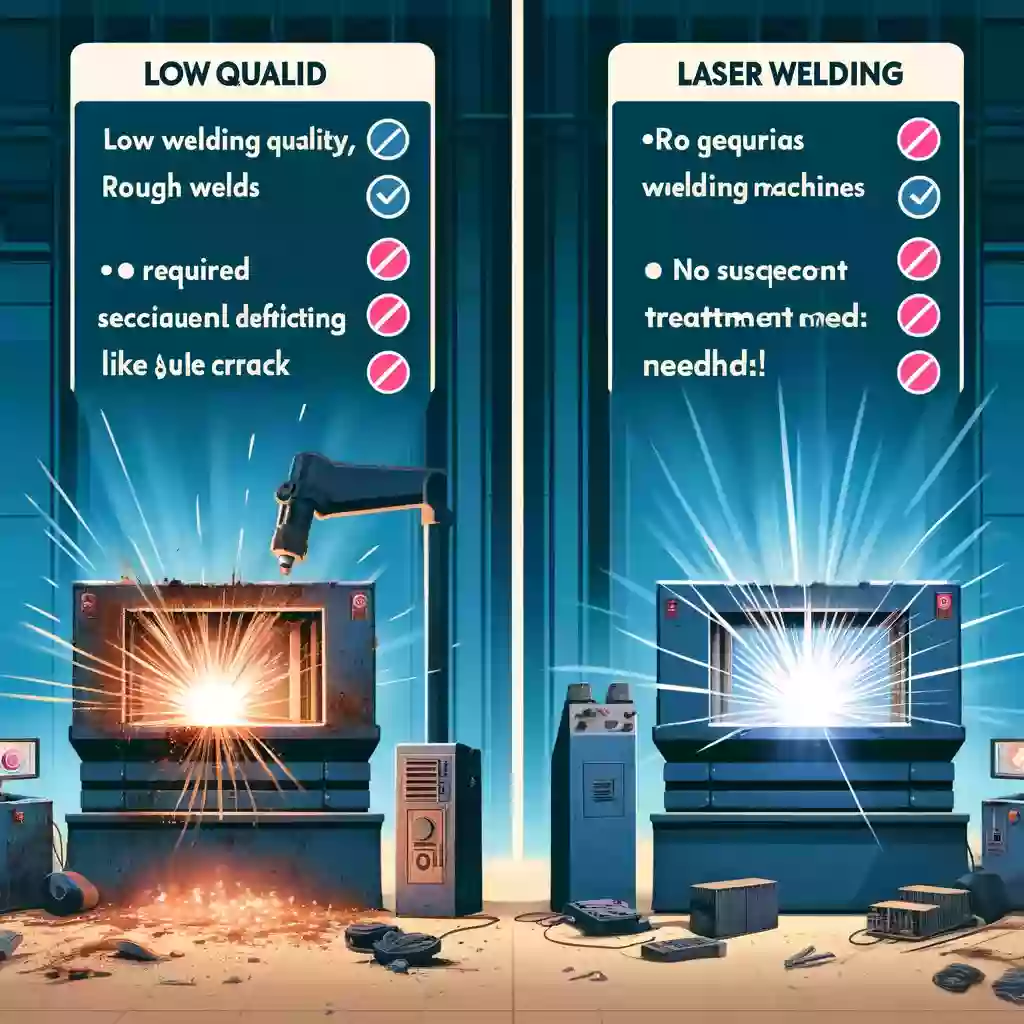
Final Thoughts
Compared with traditional welding machines, laser welding machines have obvious advantages in welding accuracy, speed, applicable materials and welding quality. However, the equipment cost of laser welding machines is relatively high, and the operating technical requirements are also higher. Therefore, in some cost-sensitive or low-tech occasions, traditional welding machines still have their value. With the continuous advancement of science and technology and the maturity of application technology, laser welding technology will be more and more widely used in various industries, providing more efficient and reliable welding solutions for the development of the manufacturing industry.